Optimize Product Development with Teamcenter
Make your manufacturing and Engineering-to-Order projects smoother with Siemens Teamcenter. Teamcenter helps you work better together, cut costs, and scale as your needs change.
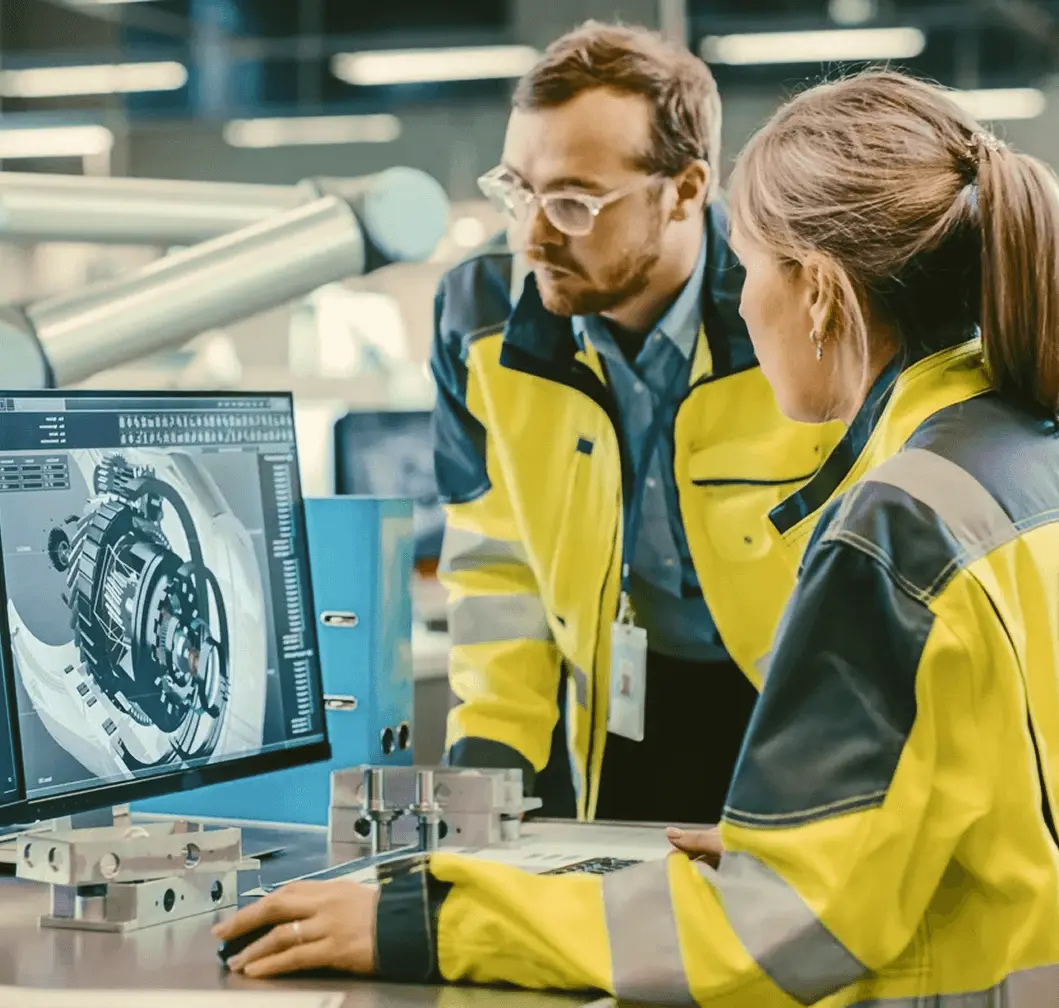
The CLEVR way: From vision to value
At CLEVR, we don’t just implement technology—we enable transformation. Our approach ensures that companies don’t just digitize but truly evolve by embedding Low Code, PLM, and MOM solutions in a structured, scalable way.
Key NX Features
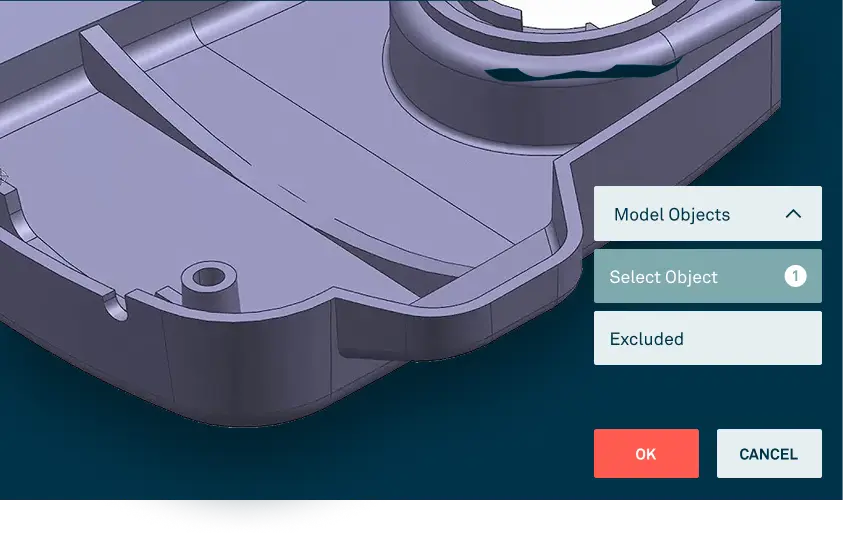
Integrated Design, Simulation, and Manufacturing
Combine all aspects of product development into a single environment, reducing design iterations and accelerating time-to-market.
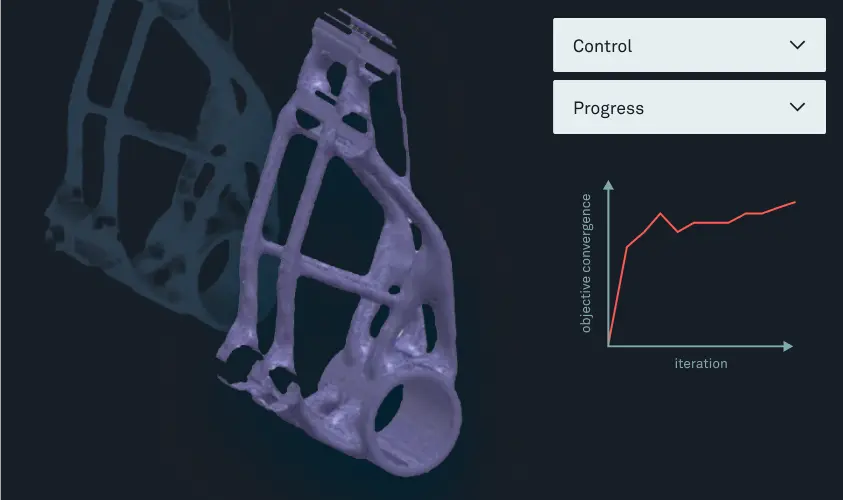
Integrated Design, Simulation, and Manufacturing
Combine all aspects of product development into a single environment, reducing design iterations and accelerating time-to-market.
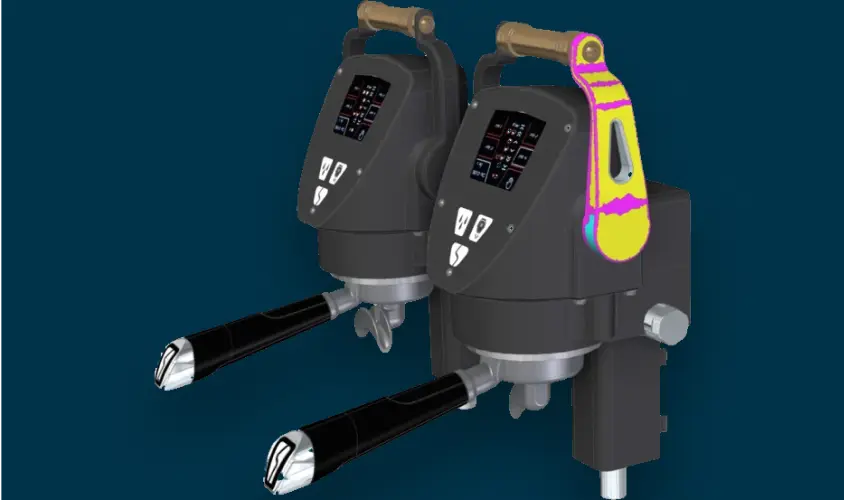
Integrated Design, Simulation, and Manufacturing
Combine all aspects of product development into a single environment, reducing design iterations and accelerating time-to-market.
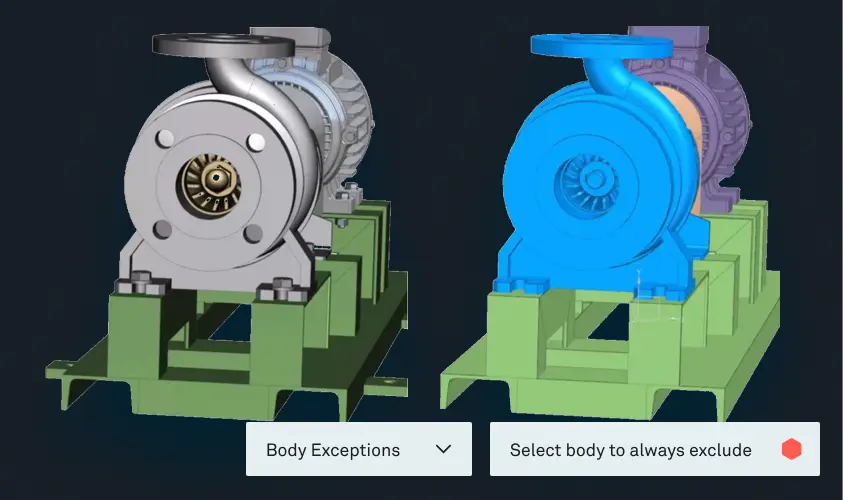
Integrated Design, Simulation, and Manufacturing
Combine all aspects of product development into a single environment, reducing design iterations and accelerating time-to-market.
Why CLEVR?
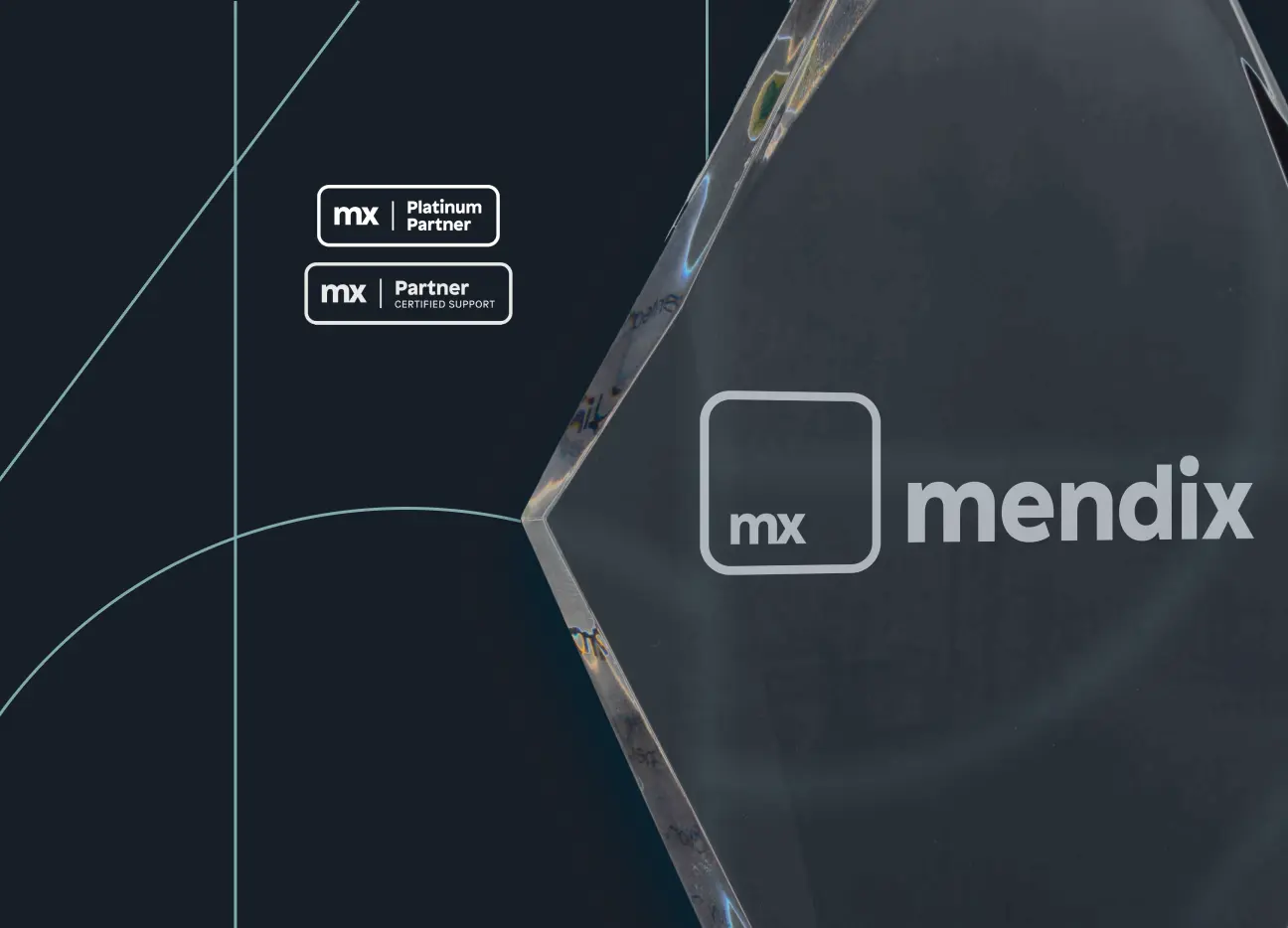
- Proven Expertise: 20 years of low code experience, 3,500+ applications delivered.
- Tailored Solutions: A unique "Vision to Value" methodology ensuring measurable results.
- Global Recognition: Mendix Platinum Partner, awarded Best BNL Partner 2024.
- Customer Satisfaction: Score of 8.8 out of 10, reflecting our commitment to excellence.
- Certified Professionals: The largest team of Mendix expert developers and MVPs.
- Proven Expertise: 20 years of low code experience, 3,500+ applications delivered.
Compare licensing plans
Advanced
Create and edit designs of typical 3D parts and assemblies and more with NX X Design Standard.
Standard
Create and edit designs of typical 3D parts and assemblies and more with NX X Design Standard.
Premium
Create and edit designs of typical 3D parts and assemblies and more with NX X Design Standard.
Stories from our customers
See how businesses like yours are transforming with CLEVR.
Mendix allows us to rapidly adapt to new legal demands and security updates.
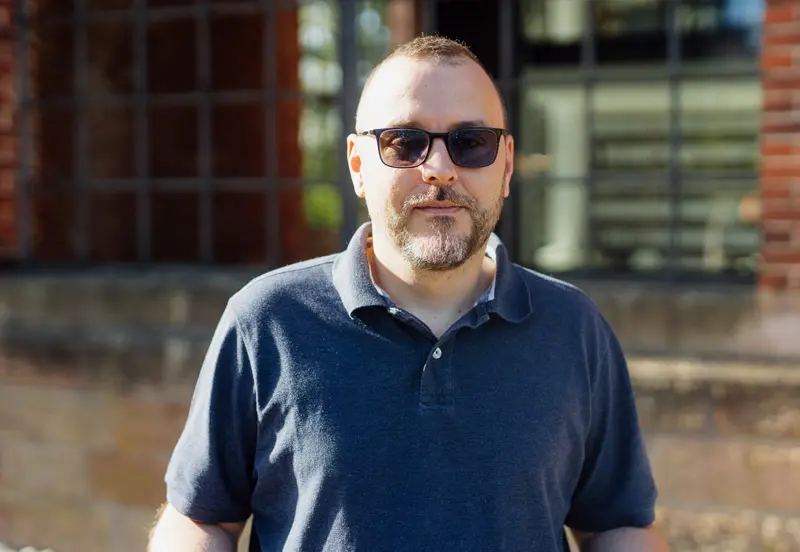
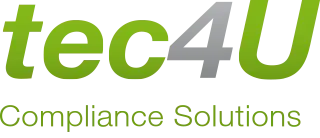
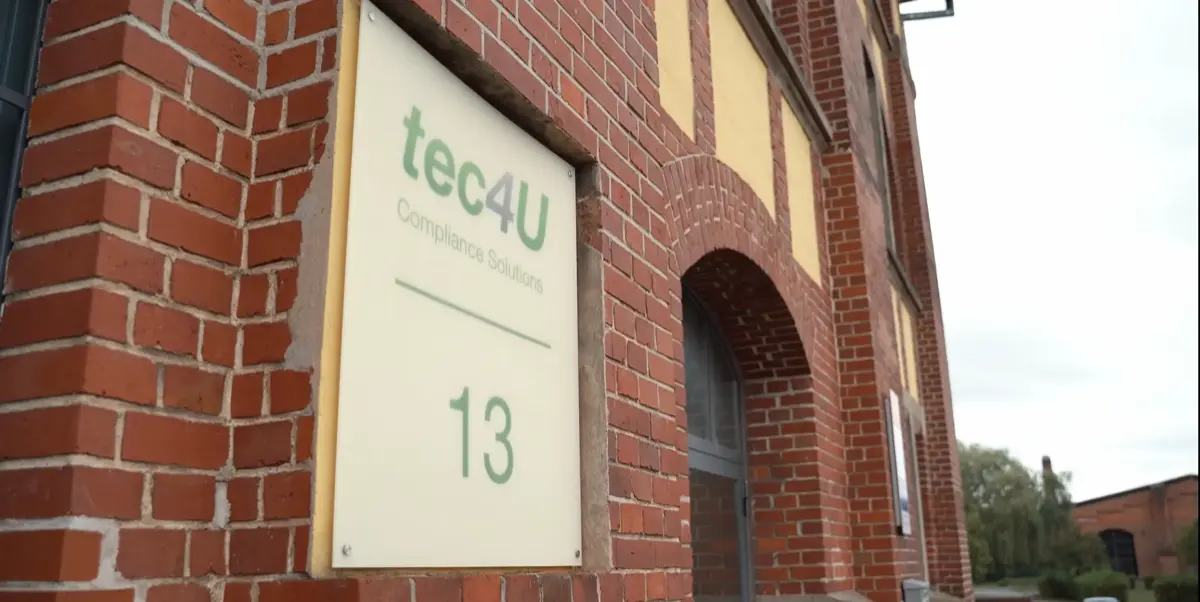
I think we build tomorrow together in different ways. We try to build the future by providing equipment to produce green hydrogen to enable the green transition, and CLEVR with the information technology will help us to do that efficiently
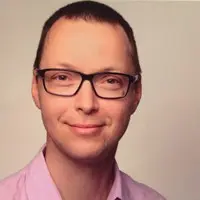
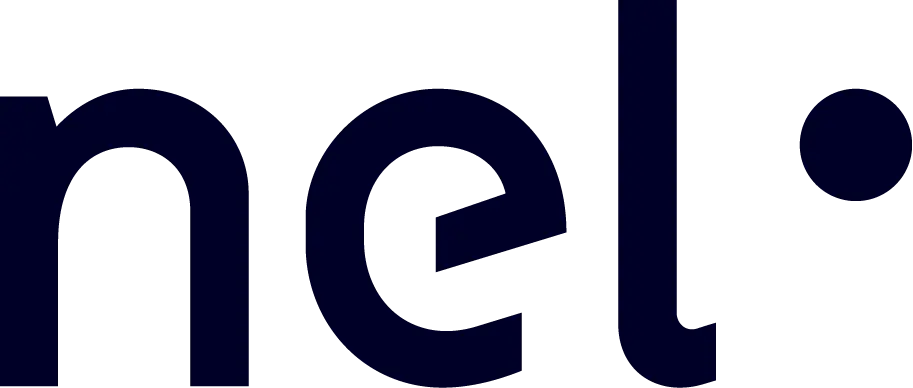
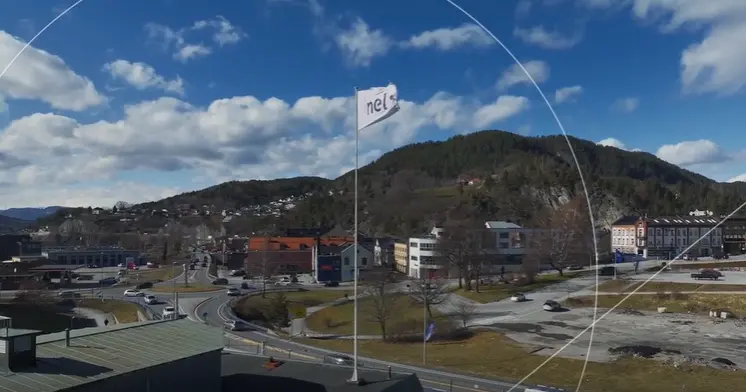
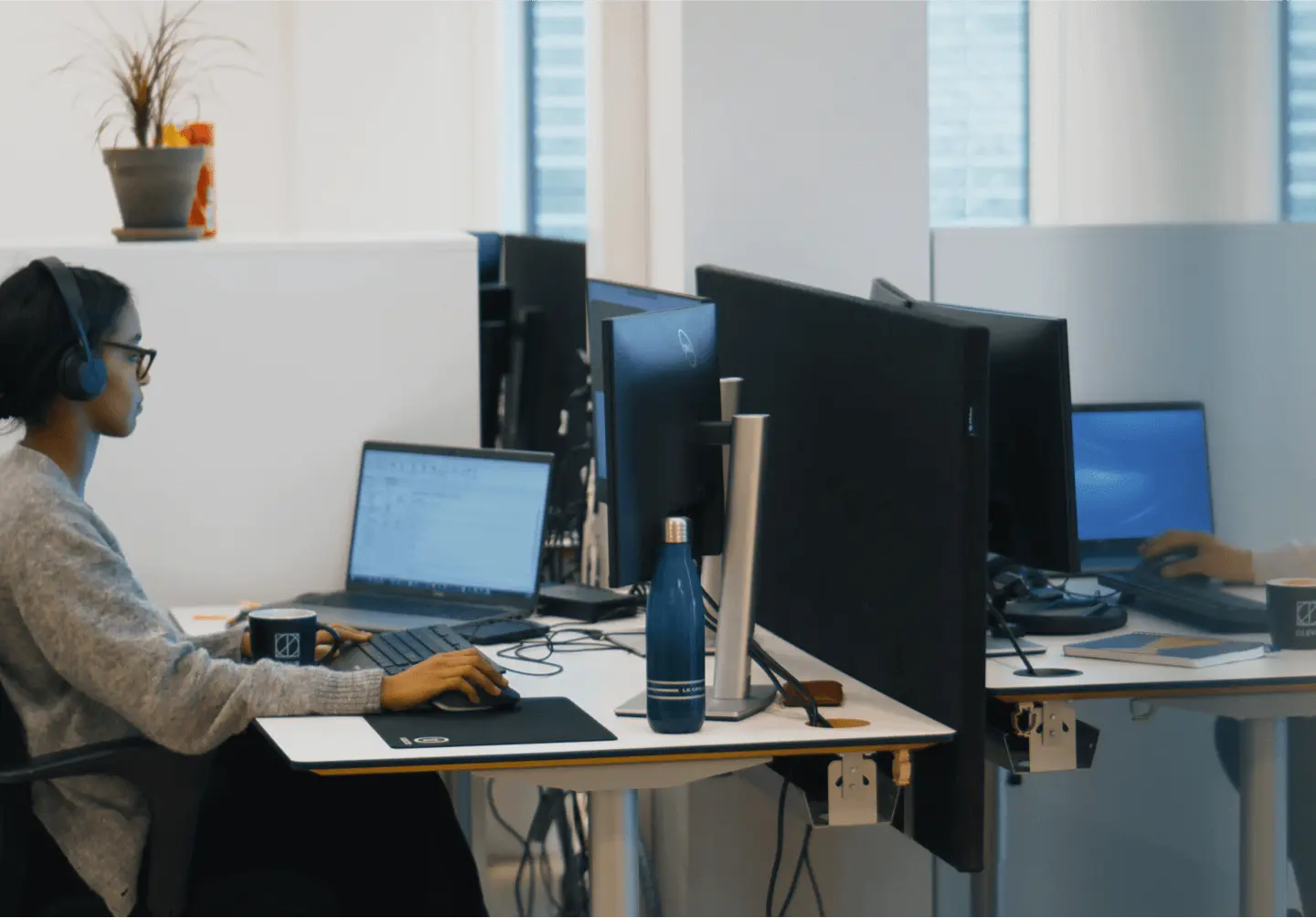
Find out how CLEVR can drive impact for your business
We try to build the future by providing equipment to produce green hydrogen to enable the green transition.
Related Resources
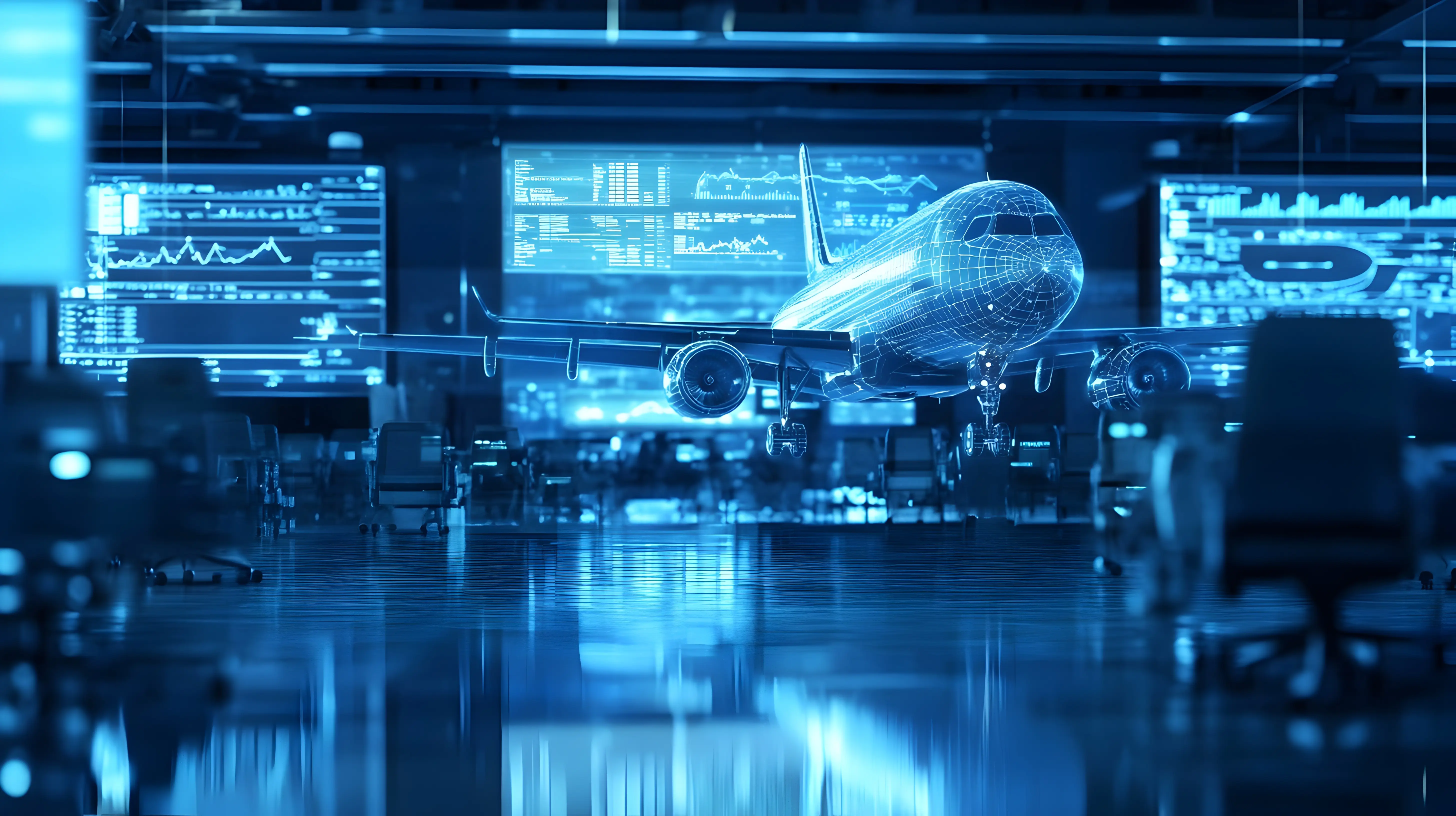
Ensuring Traceability and Regulatory Compliance in Aerospace and Defense
Every component in aerospace and defense manufacturing carries immense responsibility. A single missing traceability record or compliance gap can ground aircraft, delay vital defense programs, and put lives at risk. Quality teams spend countless hours maintaining documentation across complex supply chains while compliance officers navigate regulations that carry severe penalties for violations.
The good news is that advanced product lifecycle management (PLM) platforms offer practical ways to automate these complex requirements. This article shows you how to strengthen your traceability and compliance programs while reducing the burden on your teams.
Short on Time? Here’s a Brief Overview
- Missing or incomplete traceability records lead to costly production delays and compliance violations.
- Aerospace and defense regulations continuously evolve and require flexible systems that can quickly adapt while maintaining strict documentation.
- PLM systems provide a single source of truth for product data, streamline documentation, and connect disparate systems.
- Organizations using integrated PLM solutions can expect significant reductions in compliance-related delays.
The Importance of Traceability in Aerospace and Defense
When a critical part fails in an aircraft or defense system, manufacturers need to know exactly where that component came from, who handled it, and which other systems might have similar parts. This complete history—from raw materials through manufacturing, assembly, delivery, and maintenance—forms the foundation of traceability. Without it, a single missing record or counterfeit part can ground entire fleets, halt military operations, and put lives at risk.
We only have to look at the discovery of counterfeit components in aircraft engines in 2023. The investigation revealed these parts had entered the supply chain through multiple tiers of suppliers, affecting major airlines worldwide. From this example alone, it’s clear that maintaining a chain of documentation is imperative for safety.
For defense contractors, military equipment often requires decades of maintenance support, making detailed component histories essential for long-term sustainment. Defense manufacturers must track physical components and technical data to comply with strict security regulations across various jurisdictions. In the US, for example, this includes International Traffic in Arms Regulations (ITAR), while European manufacturers must comply with similar export control regulations.
In short, traceability protects both manufacturers and customers. When quality issues arise, manufacturers can quickly pinpoint affected components and trace them to specific production batches, suppliers, or manufacturing processes.
The Challenges of Regulatory Compliance
Aerospace and defense manufacturers face mounting pressure to manage vast amounts of compliance data while maintaining perfect accuracy. A single oversight can trigger severe consequences, such as:
- Financial penalties reaching millions of dollars
- Program delays causing ripple effects through defense supply chains
- Loss of certifications halting production lines
- Reputational damage affecting future contract opportunities
They must also navigate various regulations, including:
ITAR and export controls
Export control regulations like ITAR govern how defense-related items and technical data move across borders. For manufacturers, this means tracking:
- Component origins down to the raw material level
- Employee nationalities and security clearances
- Access controls for technical documentation
- Export licenses and agreements
- Data storage locations and transfer methods
A single ITAR violation can result in fines of up to $1 million per incident and criminal penalties. Beyond monetary costs, violations can lead to the revocation of export privileges, effectively shutting down international operations.
AS9100 quality management
AS9100 builds on ISO 9001 standards to address aerospace-specific requirements. The standard emphasizes:
- Design controls that document every engineering decision
- Risk management across the entire supply chain
- Configuration management to track product variations
- First article inspection processes
- Systems to prevent counterfeit parts
Meeting AS9100 requirements involves creating and maintaining detailed documentation at every step. For example, initial article inspection reports must verify that production processes consistently meet design specifications. That requires careful coordination between engineering, production, and quality teams.
Aviation authority requirements
Aviation authorities worldwide maintain strict oversight of manufacturing through comprehensive regulations. In the US, the Federal Aviation Administration (FAA) enforces 14 CFR Part 21, while the European Union Aviation Safety Agency (EASA) oversees European manufacturing. These frameworks require the following:
- Production records showing compliance with approved designs
- Component life tracking systems
- Maintenance documentation
- Airworthiness certification records
These requirements don’t exist in isolation—they form an interconnected web of compliance obligations. A single component might need to satisfy multiple export controls, quality requirements, and airworthiness standards simultaneously, making aerospace and defense compliance extremely challenging.
How PLM Systems Address These Challenges
Product lifecycle management (PLM) systems manage product information and processes throughout the entire product lifecycle—from initial concept through design to eventual retirement. Modern PLM systems make complex aerospace and defense manufacturing programs manageable even as regulations grow more demanding. Here’s what they offer:
A single source of truth
Modern aerospace and defense manufacturing generates massive amounts of product data. Without a central system, this information ends up scattered across departmental databases, spreadsheets, and paper files. PLM solves this by creating one authoritative source for all product information.
A good PLM system can track:
- Complete component histories from design through retirement
- Design documentation with full revision control
- Manufacturing process specifications and controls
- Quality control records and test data
- Supplier certification and compliance documentation
- Maintenance and service records
When an auditor or customer requests documentation, you can instantly pull up the complete record. You’ll know it’s accurate and up-to-date because everyone works from the same central system.
Configuration management
Aircraft and defense systems are often built in several configurations, each with specific components, documentation, and compliance requirements. PLM systems shine at managing this complexity.
Take a military aircraft program as an example. Each customer will require different avionics packages, weapons systems, or communication gear. Every variation needs its own set of documentation and certifications. A PLM system will track:
- Multiple product variants and versions
- Links between components and their documentation
- Engineering changes and downstream effects
- Customer-specific configurations
- Compliance requirements for each configuration
When an engineering change occurs, the system automatically identifies every affected configuration and updates the relevant documentation.
Supply chain integration
The aerospace and defense supply chain spans continents and includes thousands of suppliers. PLM systems help you maintain visibility and control across this complex network.
With a PLM platform, you can:
- Share technical data securely with suppliers
- Track supplier qualifications and certifications
- Monitor component quality metrics in real time
- Push change notifications instantly across the network
- Document supplier compliance with regulatory requirements
These capabilities made an enormous difference during recent supply chain disruptions. Manufacturers using PLM could quickly identify affected components and activate alternative suppliers while maintaining complete documentation of changes.
Automated quality processes
Quality management in aerospace and defense requires meticulous attention to detail. PLM systems automate many of these processes, reducing human error while speeding up routine tasks.
For quality management teams, this means automated:
- First article inspection reports
- Non-conformance tracking
- Corrective and preventive actions
- Audit scheduling and documentation
- Certification review reports
Take a first article inspection as an example. When manufacturing a new component, you must verify that the production process consistently meets design specifications. A PLM system can automatically generate inspection requirements based on the design. It can also track measurements, flag deviations, and compile the final report. All the while, it’s keeping a complete audit trail. This automation doesn’t replace human expertise—it amplifies it.
The Broader Impact of Strong Compliance
While meeting regulatory requirements is the primary goal, robust compliance systems deliver additional benefits that strengthen the entire organization. These include:
Operational efficiency
When compliance becomes automated and systematic rather than manual and reactive, operations improve across the board.
Development cycles speed up because teams spend less time on compliance paperwork, and quality improves through consistent application of standards. Supply chain management becomes more efficient with better visibility, while maintenance planning benefits from complete component histories.
Higher customer trust
Strong compliance programs build credibility with customers, regulators, and partners. This translates into:
- Faster approvals for new contracts and certifications
- Reduced scrutiny during audits
- Stronger relationships with key customers
- Better positioning for new business opportunities
Opportunities for innovation
Perhaps most importantly, when basic compliance tasks become automatic, teams can focus their energy on innovation.
Engineers can spend more time on design improvements, while quality teams can work on process optimization. Supply chain managers can explore new partnerships, and leadership can focus on strategic initiatives.
The shift from manual compliance to automated systems creates space for the creative thinking that drives aerospace and defense innovation forward.
Final Thoughts
Achieving perfect traceability and compliance in aerospace and defense might seem impossible. The regulations keep changing, supply chains grow more complex, and the stakes get higher every year. But manufacturers who embrace modern solutions like PLM systems are showing it’s possible to turn these challenges into opportunities for improvement.
Start by examining where manual processes and disconnected systems create operational risks. Then, explore how PLM solutions could help automate and streamline these areas. CLEVR’s complete guide to PLM offers practical insights to help you get started.
Research Methodology
This article draws on extensive research into aerospace and defense regulations, traceability requirements, and compliance best practices. Findings reflect both established standards and new developments in regulatory technology.
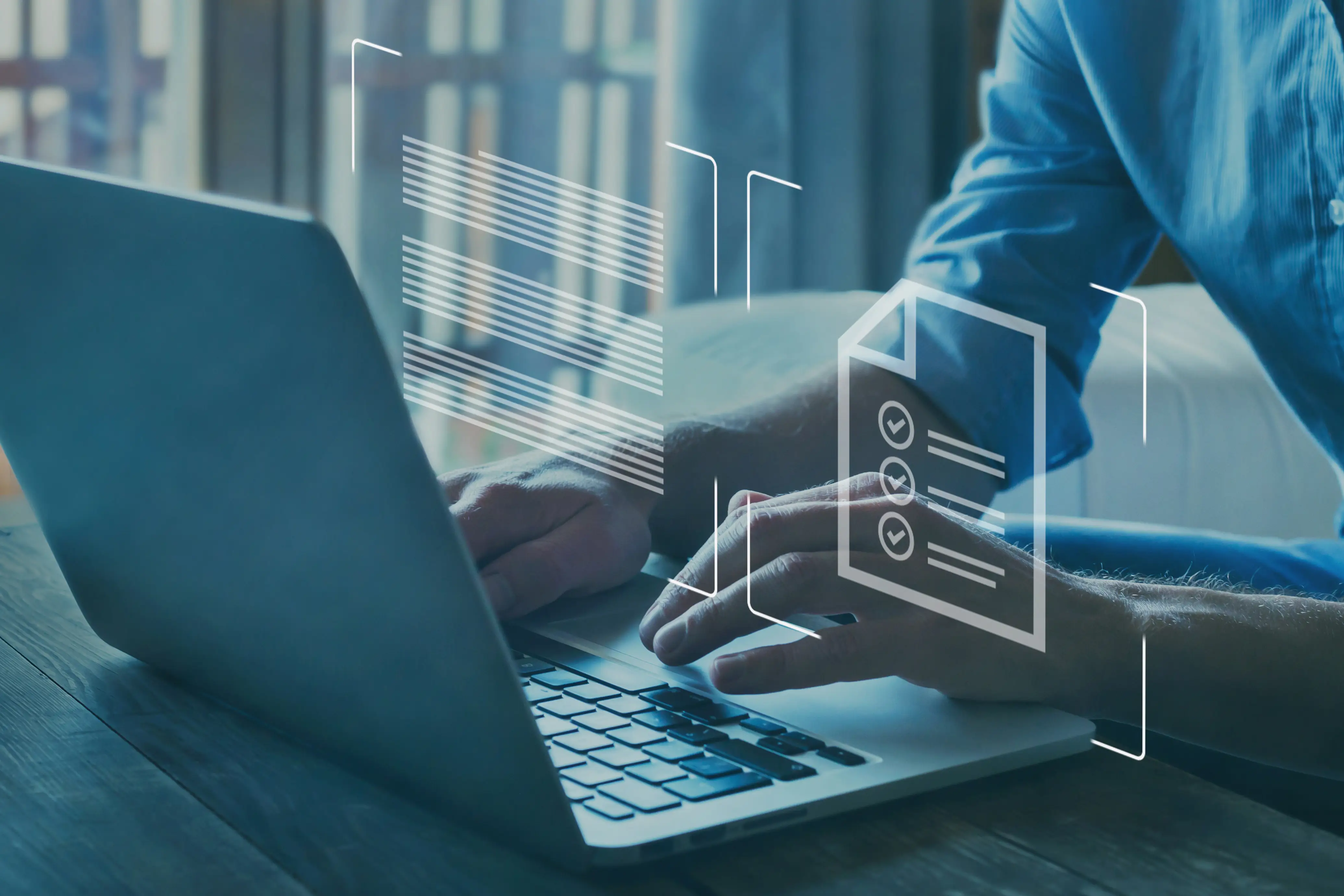
Dual-Use Compliance: The Hidden Cost of Getting It Wrong in Aerospace and Defense
For European aerospace and defense companies, dual-use compliance is business survival. One export control error can freeze shipments, cancel contracts, and trigger penalties in the millions. With regulations tightening across the EU following geopolitical shifts, companies handling items with both civilian and military applications face unprecedented scrutiny.
The costs of getting compliance wrong extend far beyond fines, creating ripple effects through operations, reputation, and market access. Let's look at why forward-thinking organizations are discovering that robust compliance can be a competitive edge.
Short on Time? Here's a Brief Overview
- Dual-use items account for 2.5% of total EU exports, valued at approximately €147 billion annually.
- A single documentation gap can trigger investigations and penalties even when physical exports were properly licensed.
- Sanctions violations can result in fines of up to 5% of worldwide turnover or fixed penalties up to €40 million.
- Modern PLM systems reduce compliance processing time while minimizing the risk of non-compliance.
The Risks of Non-Compliance
According to the European Commission's official statistics, dual-use items account for roughly 2.5% of total EU exports, with a value of approximately €147 billion in 2021. The same report indicates that the EU processed applications for dual-use trade valued at €45.5 billion, with 568 applications being denied despite the reported high approval rate.
With dual-use items being such a significant part of trade, there's a careful balance that regulators must maintain between facilitating legitimate trade and enforcing security controls.
1. Fines and legal penalties
Under EU Directive 2024/1226, companies breaching sanctions face fines of 1% to 5% of total worldwide turnover or fixed penalties between €8 million and €40 million. Intentional embargo violations result in at least one year of imprisonment, while negligent export restriction violations can incur fines up to €500,000.
2. Operational impact
There are repercussions to consider beyond potential fines. When compliance flags appear, shipments stop completely. For aerospace manufacturers in just-in-time supply chains, even a one-week customs hold can trigger contract penalties and production halts across the network.
Defense procurement increasingly favors suppliers with robust, digitally enabled compliance systems. So companies without verifiable compliance trails find themselves eliminated early from bidding processes, regardless of their technical capabilities or competitive pricing.
Once flagged for compliance issues, rebuilding trust becomes exceptionally difficult. The aerospace and defense sector operates within small networks where reputation travels quickly. A compliance failure with one customer can lock you out of entire market segments.
Real-World Compliance Failures
However important, not all companies have succeeded in implementing it correctly. These recent real-world examples bring the importance of getting dual-trade right:
- ΡTX (formerly Raytheon) reached a $200 million settlement with the US State Department for violations involving employees traveling with laptops containing sensitive military program data to sanctioned countries.
- 3D Systems faced a $2.77 million penalty for unlicensed exports of controlled aerospace technology. The violations included emailing military electronics design drawings to a Chinese subsidiary and storing controlled technology on a server in Germany.
- A 2024 case in Germany saw individuals sentenced to seven years in prison for exporting battlefield electronics to Russia via intermediaries. The court ordered the profit confiscation of €2.1 million from one individual and €3 million from a related Swiss company.
Evolving EU/NATO Standards
Dual-use regulations are continuously changing, driven by geopolitical tensions and technological advancements.
The European Commission adopted a significant update to the EU dual-use export control list in September 2024, while recent EU sanction packages targeting Russia have removed exemptions for dual-use items that could enhance military capabilities. This means that companies are now required to implement more sophisticated monitoring of end-users and end-uses.
But also regulatory authorities have moved from periodic reporting to expectations of continuous compliance readiness. Annual self-certifications are giving way to audit-ready systems that can demonstrate compliance at any moment.
Why Traditional Systems Can't Keep Up
Many aerospace companies still rely on compliance approaches designed for a different era, creating serious vulnerabilities.
Spreadsheets, shared drives, and email approvals introduce unacceptable risks. Manual classification and tracking processes inevitably produce inconsistencies as products, regulations, and teams change.
When regulators request audit trails, these fragmented systems often can’t produce the coherent evidence needed. And when engineering, compliance, and logistics operate in separate systems, critical handoffs become vulnerability points.
Design changes may not trigger compliance reviews, and compliance teams may approve configurations without visibility into recent engineering modifications.
Building Compliance into the Workflow With PLM
Product Lifecycle Management (PLM) systems transform compliance by embedding it directly into product development and management processes. Here’s how:
Compliance by design
With a modern PLM system like Siemens Teamcenter, compliance becomes an integral part of the product lifecycle. Classification and export control parameters become attributes of the product record itself, ensuring visibility at every stage from design to delivery.
Aerospace and defense companies can implement role-based access controls, ensuring only authorized personnel can view, modify, or transfer controlled information. The system maintains comprehensive audit trails of all product-related activities, creating verifiable records of who accessed information, when, and what changes were made.
Automated classification and change management
Advanced PLM systems automate much of the compliance burden through rules-based classification. When engineers modify designs, the system automatically flags potential compliance implications. And when export control regulations change, these updates can be systematically applied across the product portfolio.
Oil and gas leader Optime Subsea experienced this benefit when it implemented a PLM solution with CLEVR. Its unique engineering-to-order business model required meticulous recordkeeping and history tracking. CLEVR helped it establish uniform business processes and agile integration that streamlined supplier collaboration while ensuring data security—important for companies dealing with dual-use technology.
Single source of truth for audit readiness
The most significant advantage of PLM-enabled compliance is creating a single, authoritative source of truth for all product information. This centralized repository becomes the definitive record for regulatory documentation, component histories, and material compositions.
Nexans, one of the world's largest cable suppliers, turned to CLEVR to move its processes onto Siemens Teamcenter. With 25,000 employees in 40 countries, its previous systems often contained unreliable data that needed double-checking. Through its PLM implementation, the company improved data quality and standardized working methods—allowing staff to work faster, with greater accuracy, while maintaining compliance.
The CLEVR Approach: Compliance Without Bottlenecks
Implementing compliance-focused PLM requires both technological expertise and a deep understanding of aerospace regulatory requirements. CLEVR specializes in helping A&D companies implement Siemens Teamcenter and other PLM solutions that embed compliance into everyday workflows.
CLEVR integrates compliance requirements directly into engineering and operational processes, ensuring teams work efficiently while maintaining audit readiness. Engineering, quality, procurement, and legal departments can all work with one traceable system.
For companies operating under multiple regulatory frameworks (ITAR, EAR, EU dual-use regulations), CLEVR's implementation expertise ensures PLM systems accommodate these overlapping requirements while navigating both NATO and EU requirements.
Turn Compliance From a Cost into a Competitive Edge
Forward-thinking aerospace companies recognize that compliance excellence represents a strategic opportunity.
When properly implemented, advanced compliance capabilities become a competitive edge. Prime contractors increasingly favor suppliers who can demonstrate robust compliance systems, both to minimize their own risk exposure and to simplify their supply chain management. For tier-one and tier-two suppliers, documented compliance excellence can open doors to higher-value contracts and strategic partnerships.
Companies with mature, PLM-enabled compliance capabilities can also respond more quickly to new business opportunities. When RFPs arrive, they can immediately determine classification requirements and licensing timelines, allowing for more accurate bidding and delivery commitments.
For more information on PLM solutions for A&D, get in touch with CLEVR today.
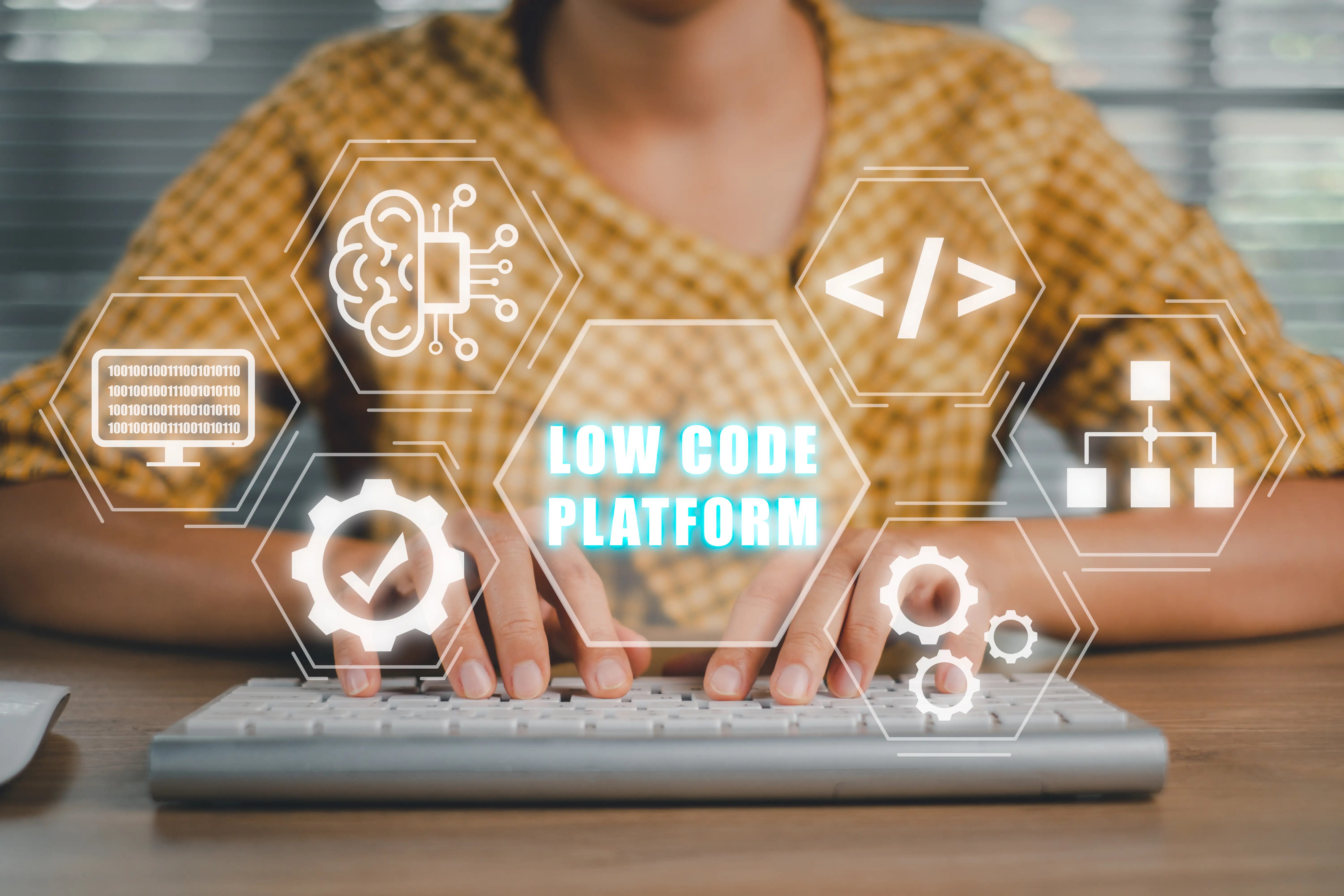
Mendix vs. OutSystems: Which Low Code Platform Wins?
Picking the right low code development platform can determine whether your B2B eCommerce succeeds or stalls.
The market moves fast, and while leaders like Mendix and OutSystems both claim they'll transform how you build applications, they work quite differently under the hood. If you're a CIO, CTO, or enterprise architect, you know how challenging it is to separate vendor marketing from reality.
Whether you need lightning-fast delivery, straightforward development, massive scalability, or robust governance, this comparison focuses on what each platform actually delivers and which one could best fit your real needs.
Short on Time? Here's a Brief Overview
- Mendix (owned by Siemens) is a cloud-native platform that uses a collaborative, visual-first method suitable for all skill levels.
- OutSystems is a full-stack low code platform focused on high-performance enterprise applications with real-code output.
- Mendix offers a more intuitive experience, making it a strong choice for non-developers, whereas OutSystems blends visual development with professional code, which means a steeper learning curve but greater depth for technical teams.
- Mendix is highly scalable, supporting both SMBs and large enterprises, with flexible cloud and hybrid deployment options.
- OutSystems has a larger marketplace with over 200 out-of-the-box integrations. Mendix supports around 100 integrations, with a stronger focus on the Siemens and SAP ecosystems.
Overview of Platforms
Mendix
Mendix built its reputation on visual, model-driven development, where applications are created using graphical models for data, logic, and user interfaces. Mendix Runtime interprets these models directly, ensuring the model remains the single source of truth. This low code platform works for a wide range of custom applications with minimal coding needed.
The core principle of Mendix's architecture is that the visual model is the definitive representation of the application. The Mendix Runtime engine doesn't generate large volumes of intermediate code; it interprets the visual models directly. This maintains consistency and simplifies long-term maintenance, as there is no generated code to manage or get out of sync with the model.
It's cloud-native from the ground up, delivering containerized, portable applications you can deploy anywhere, such as Mendix Cloud, private clouds, or public clouds like AWS and Azure. With Git-based version control and strong collaboration tools within its integrated development environment (IDE), it's built for team-based, agile projects.
OutSystems
OutSystems goes a different direction, focusing on high-performance applications by generating optimized, real-code output (C# and JavaScript) from its visual models. This gives professional developers deep control, robust DevOps capabilities, and a system that feels closer to traditional coding.
There are two main options: OutSystems 11 (which supports cloud, on-premise, and hybrid deployments) and the newer OutSystems Developer Cloud (ODC)—a cloud-native SaaS platform running on modern tech like Kubernetes and microservices. This architecture supports rapid application development for building and scaling complex, mission-essential enterprise-grade applications.
Ease of Use & Learning Curve
Mendix
Mendix typically wins the "easiest to get started" conversation, especially if you're new to low code or don't have a heavy technical background. Its visual method offers a more intuitive experience for non-developers.
Mendix Studio Pro is well-suited for everyone, from business analysts to professional developers. But as your projects get more complex, you'll face a steeper learning curve to master the advanced features.
For instance, while a business analyst might easily create initial application screens, mastering advanced features like complex data integrations, writing custom Java actions for backend logic, or building custom UI widgets with JavaScript or React requires professional developer skills.
OutSystems
OutSystems appeals more to developers who want serious tools for full-stack development. Its environment blends visual modeling with access to professional code, which can increase complexity for less technical users but is a major advantage for technical teams.
While there's more to learn upfront, professional developers often prefer the depth and control once they're up to speed. G2 user reviews give OutSystems a slight edge on ease of use over Mendix, suggesting that technical users adapt well to its power.
Scalability & Enterprise Readiness
Both platforms handle large enterprise demands, but they scale differently.
Mendix
Mendix works for a wide range of organizations, from SMBs to large enterprises, offering flexible cloud and hybrid deployment options. It uses stateless runtimes and microservices support for horizontal scaling that grows with your user base. Its flexible deployment options let you tap into auto-scaling and load-balancing from major cloud providers.
The platform's architecture supports deployment on various cloud environments, including AWS, Azure, and Google Cloud, allowing organizations to utilize the native auto-scaling capabilities of these providers. Mendix for Private Cloud is also compatible with various Kubernetes and OpenShift distributions.
OutSystems
OutSystems, on the other hand, excels in raw enterprise-grade performance and auto-scaling. With its Kubernetes foundation, ODC delivers high availability and resilience for mission-essential applications built to serve millions of users.
The architecture is designed to handle high volumes of users and substantial data, making it a popular choice for core system modernization. If your primary concern is building systems that can handle extreme performance demands automatically, OutSystems has an advantage.
Integration & Extensibility
Mendix
Mendix provides solid tools for creating seamless integrations with enterprise systems, especially if you're already invested in the Siemens ecosystem. It supports hundreds of integrations and connects particularly well with Siemens Teamcenter PLM and SAP, making it a natural choice for organizations already using those systems.
Mendix Connect gives you a catalog for discovering and using data from various enterprise sources. For anything not covered, you can build custom code extensions.
Developers can write custom backend logic using Java actions and build custom UI widgets using JavaScript or React. Mendix also provides platform APIs and an SDK (Model SDK) for programmatic interaction with the platform itself, allowing integration with external tools.
OutSystems
OutSystems responds with the OutSystems Forge—a huge ecosystem of pre-built components and connectors. It boasts over 200 out-of-the-box integrations and over 5,000 reusable assets. This extensive library makes integration with popular systems, such as Salesforce, Oracle, and Microsoft Dynamics, much simpler.
Beyond the Forge, deep extensibility is managed through Integration Studio, a tool where developers can write C#/.NET code to create "Extensions." These can then be used visually as components within the main Service Studio IDE.
Development Features & Collaboration
Mendix
Mendix Studio Pro serves as an integrated development environment with comprehensive visual tools for creating custom applications. Its key features include graphical modeling of data, UI pages, and application logic through microflows (for server-side logic) and nanoflows (for client-side logic).
It has integrated Git-based version control, which is essential for modern, collaborative development. It supports multi-experience UI for web and mobile apps and offers strong tools to encourage business-IT collaboration throughout the iterative development process.
While it's primarily a low code platform, you can extend functionality with Java for backend work and JavaScript or React for UI customization.
OutSystems
OutSystems' Service Studio enables visual full-stack development across UI, application logic, and data models. It's built on a modular architecture that promotes the reuse of pre-built templates and components.
Two standout key features are the "One-Click Publish" function, which compiles, deploys, and manages database updates automatically, and the TrueChange engine, which provides real-time validation and dependency analysis to catch errors instantly and reduce debugging headaches.
With AI-assisted development features and workflows designed for enterprise-level scale, it's a powerful environment for professional teams.
Pricing & Total Cost of Ownership
Both Mendix and OutSystems use pricing models that require custom quotes for enterprise deployments.
Mendix
Mendix offers more transparent pricing with user-based tiers, starting with a free plan and scaling up. Costs are based on the number of users, applications, and required support levels.
For the Standard and Premium tiers, the cost of the underlying cloud compute resources (e.g., from AWS or Azure) is typically separate from the license and must be budgeted for independently.
OutSystems
OutSystems generally has higher licensing costs, which makes sense given its focus on large-scale, mission-essential applications. Pricing is primarily based on Application Objects (a measure of application size) and user counts.
An Application Object (AO) is an OutSystems-specific metric that represents the sum of functional elements, such as screens, database tables, and API methods. A typical medium-sized app is estimated to have around 150 AOs. This value-based pricing contributes to its perception as a premium-priced platform, as well as the opaque nature of its pricing.
Community, Support & Ecosystem
Mendix
Mendix maintains an active community forum and provides extensive documentation through Mendix Academy and GitHub. Its marketplace is growing and well-supported, and its alignment with Siemens provides a strong backing and a clear focus for its ecosystem, especially in industrial sectors.
The Mendix Academy offers a wealth of online training materials and official certification paths to help developers build their skills, complementing the community forums where a high percentage of questions are answered promptly.
OutSystems
OutSystems has an even bigger, active global community of hundreds of thousands of members. This strong developer community is a significant asset, providing extensive learning resources and peer support.
The OutSystems Forge is a major advantage here. The vast repository of free, reusable assets can dramatically cut development time, allowing development teams to solve common challenges without reinventing the wheel.
Which Platform Suits Your Team?
Both Mendix and OutSystems are excellent choices for an enterprise low code development platform. The decision between Mendix and OutSystems comes down to your organization's specific context. To help clarify the decision, consider the following scenarios:
Scenario | Primary need | Recommended platform | Why? |
---|---|---|---|
SMB | Simplicity, quick adoption, mixed-skill teams | Mendix | Offers a more intuitive experience for non-developers and provides flexible hybrid deployment options suitable for smaller-scale operations. |
Enterprise-scale, performance-critical | High performance, mission-critical reliability, auto-scaling | OutSystems | Architected for extreme scalability and performance, making it ideal for core systems and applications that cannot fail. |
Mixed-requirement environments | Balance of usability, integration, and developer control | Weigh the factors | If your ecosystem is heavily based on SAP/Siemens, Mendix has the edge. If you have a professional developer team needing deep control and access to a vast component library, OutSystems is likely the better fit. |
Final Thoughts
Both Mendix and OutSystems are formidable low code development platforms capable of delivering transformative results. The best decision comes from a balanced evaluation of your organization's needs, your development team's maturity, and your long-term strategic goals.
To move forward, we recommend hands-on evaluation. Engage with both vendors, request tailored demos for your specific use cases, and most importantly, conduct proof-of-concept projects. This provides your team with practical experience on each platform and offers the clarity needed for confident decision-making.
For organizations requiring custom applications, partnering with an experienced provider like CLEVR can offer guidance and expertise to navigate this process, ensuring a successful implementation that delivers measurable business value.
Research Methodology
The information reflects platform and market conditions as of mid-2025. This article draws from a detailed analysis of independent sources, including market research from leading analyst firms like Gartner and Forrester, user review platforms like G2 and TrustRadius, and documented case studies. We focused on providing a neutral, credible comparison based on real-world user experiences and expert analysis.
Frequently Asked Questions
Which industries does CLEVR serve?
Lorem ipsum dolor sit amet, consectetur adipiscing elit. Suspendisse varius enim in eros elementum tristique. Duis cursus, mi quis viverra ornare, eros dolor interdum nulla, ut commodo diam libero vitae erat. Aenean faucibus nibh et justo cursus id rutrum lorem imperdiet. Nunc ut sem vitae risus tristique posuere.
How does CLEVR support digital transformation?
Lorem ipsum dolor sit amet, consectetur adipiscing elit. Suspendisse varius enim in eros elementum tristique. Duis cursus, mi quis viverra ornare, eros dolor interdum nulla, ut commodo diam libero vitae erat. Aenean faucibus nibh et justo cursus id rutrum lorem imperdiet. Nunc ut sem vitae risus tristique posuere.
What is CLEVR's experience and reach?
Lorem ipsum dolor sit amet, consectetur adipiscing elit. Suspendisse varius enim in eros elementum tristique. Duis cursus, mi quis viverra ornare, eros dolor interdum nulla, ut commodo diam libero vitae erat. Aenean faucibus nibh et justo cursus id rutrum lorem imperdiet. Nunc ut sem vitae risus tristique posuere.
Who are some of CLEVR's notable clients?
Lorem ipsum dolor sit amet, consectetur adipiscing elit. Suspendisse varius enim in eros elementum tristique. Duis cursus, mi quis viverra ornare, eros dolor interdum nulla, ut commodo diam libero vitae erat. Aenean faucibus nibh et justo cursus id rutrum lorem imperdiet. Nunc ut sem vitae risus tristique posuere.