Transform Manufacturing Processes with PLM
Build better manufacturing workflows with PLM software that seamlessly bridges the gaps between conception, launch, and servicing. With MES and AI, CLEVR's PLM solutions use the latest technology to create exactly the right workflows.
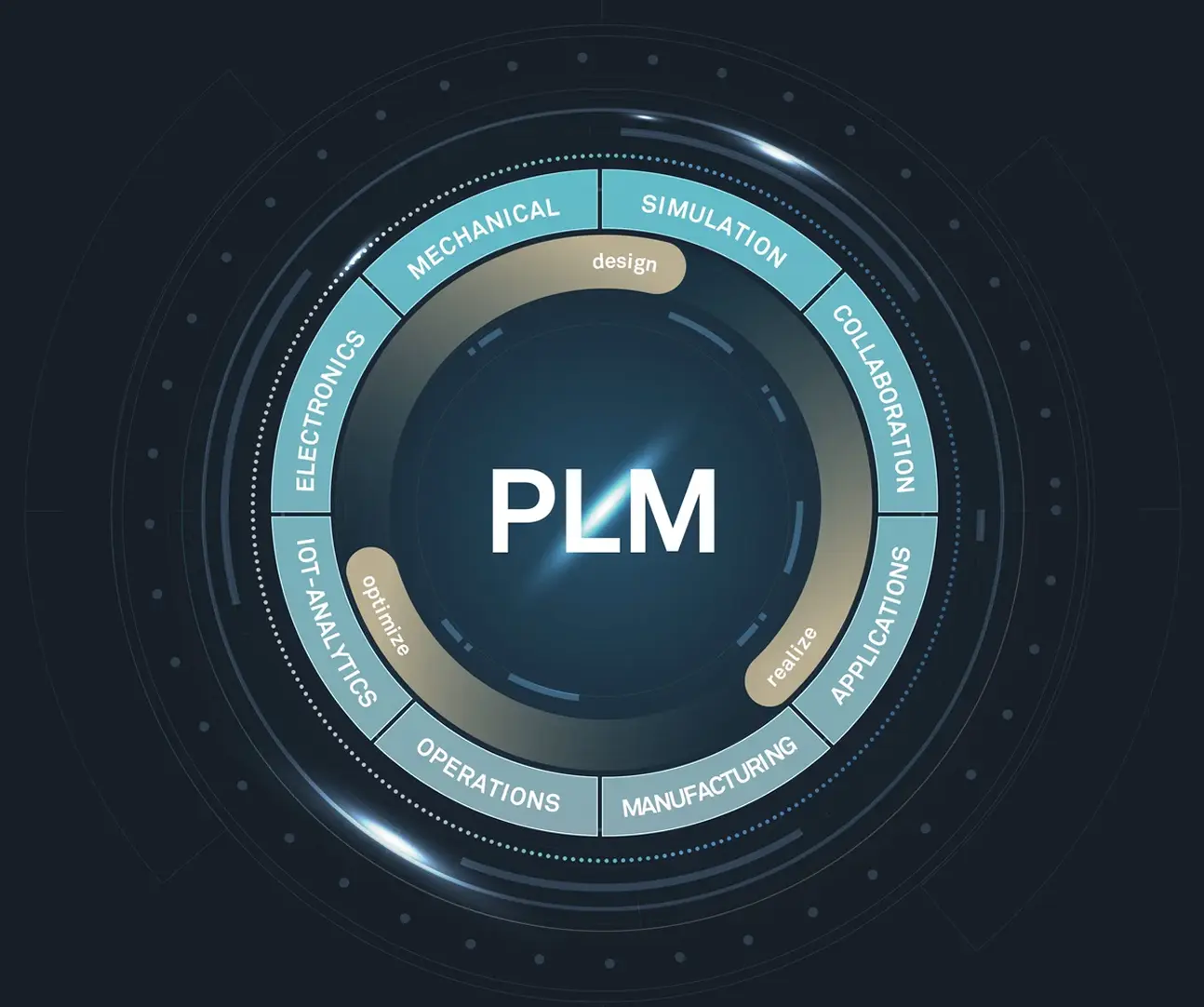
A Single Source of Truth
Low code enhances Product Lifecycle Management by offering custom applications that seamlessly connect with other systems, often with automation. Automating certain PLM stages streamlines delivery, supports the development of mobile and native PLM apps, and helps manufacturers handle complex use cases by leveraging information from multiple sources.
End-to-End Efficiency: From Conception To Retirement
Concept and Design
Experience faster product design cycles with an advanced CAD system that features virtual prototyping in 2D and 3D environments. This system integrates robotics, 3D printing, and quality inspection operations. The NX integrated design and manufacturing capabilities offer an effective platform for efficient product development.
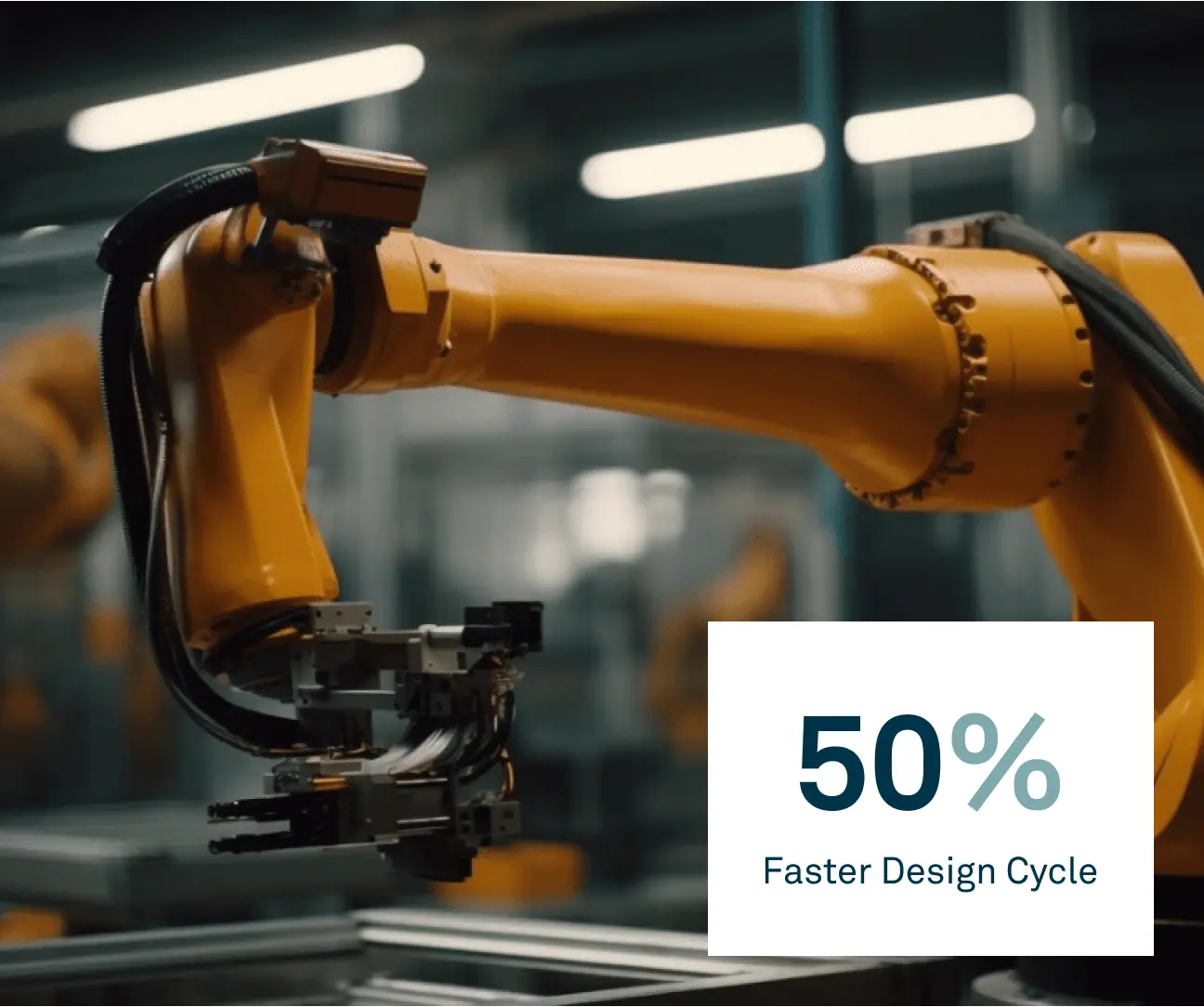
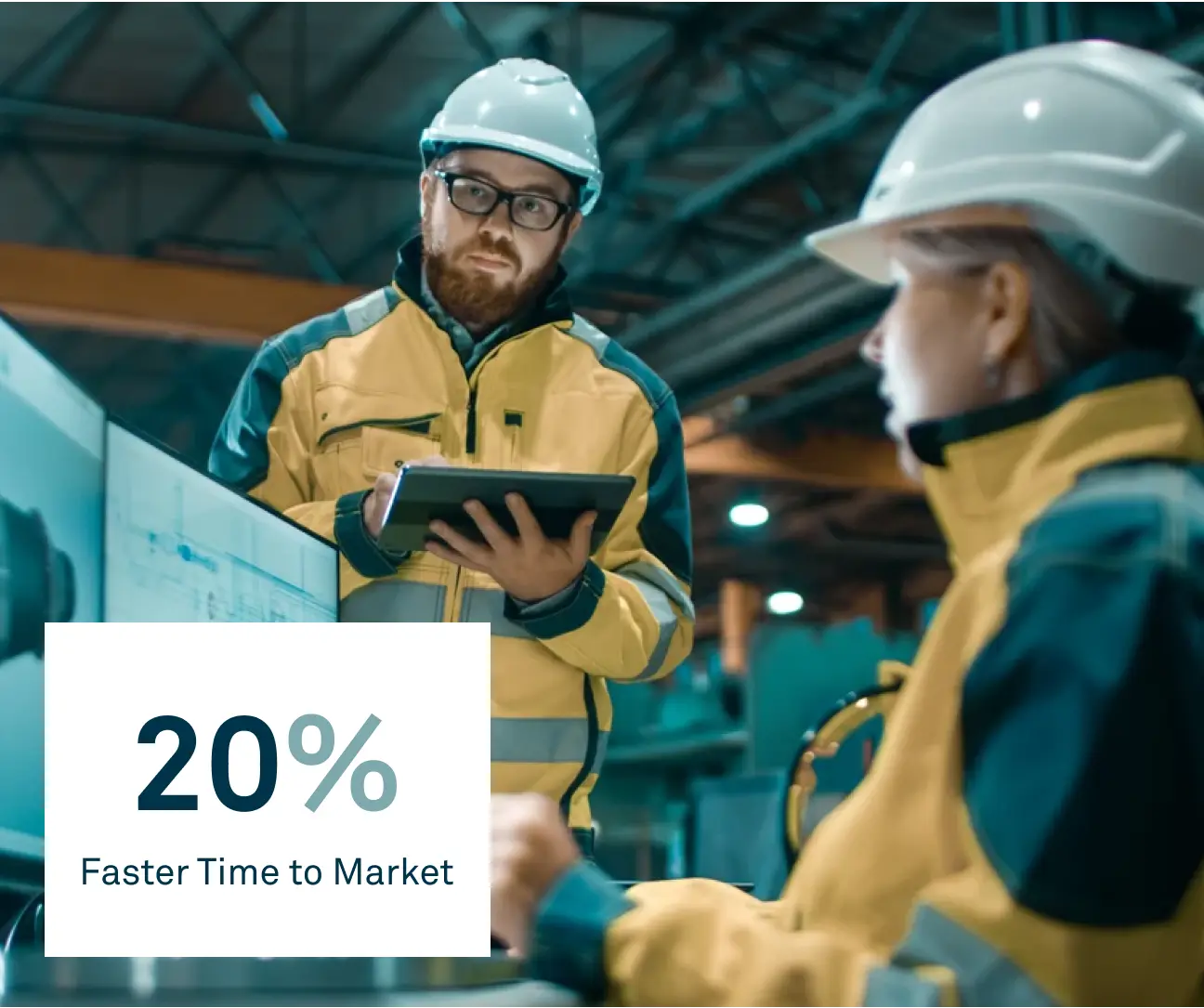
Engineering and Development
Reducing product development errors necessitates coordinating engineering with other departments and leveraging technologies like digital twins and simulation. Teamcenter accelerates the process from design to field testing, fostering collaboration, enhancing product quality, and contributing to a faster time-to-market
People and Processes
Empower teams with PLM to bridge gaps for informed decisions and seamless data flow. It features a business process modeler, change management, and an interactive dashboard to fuel innovation and enhance organizational efficiency.
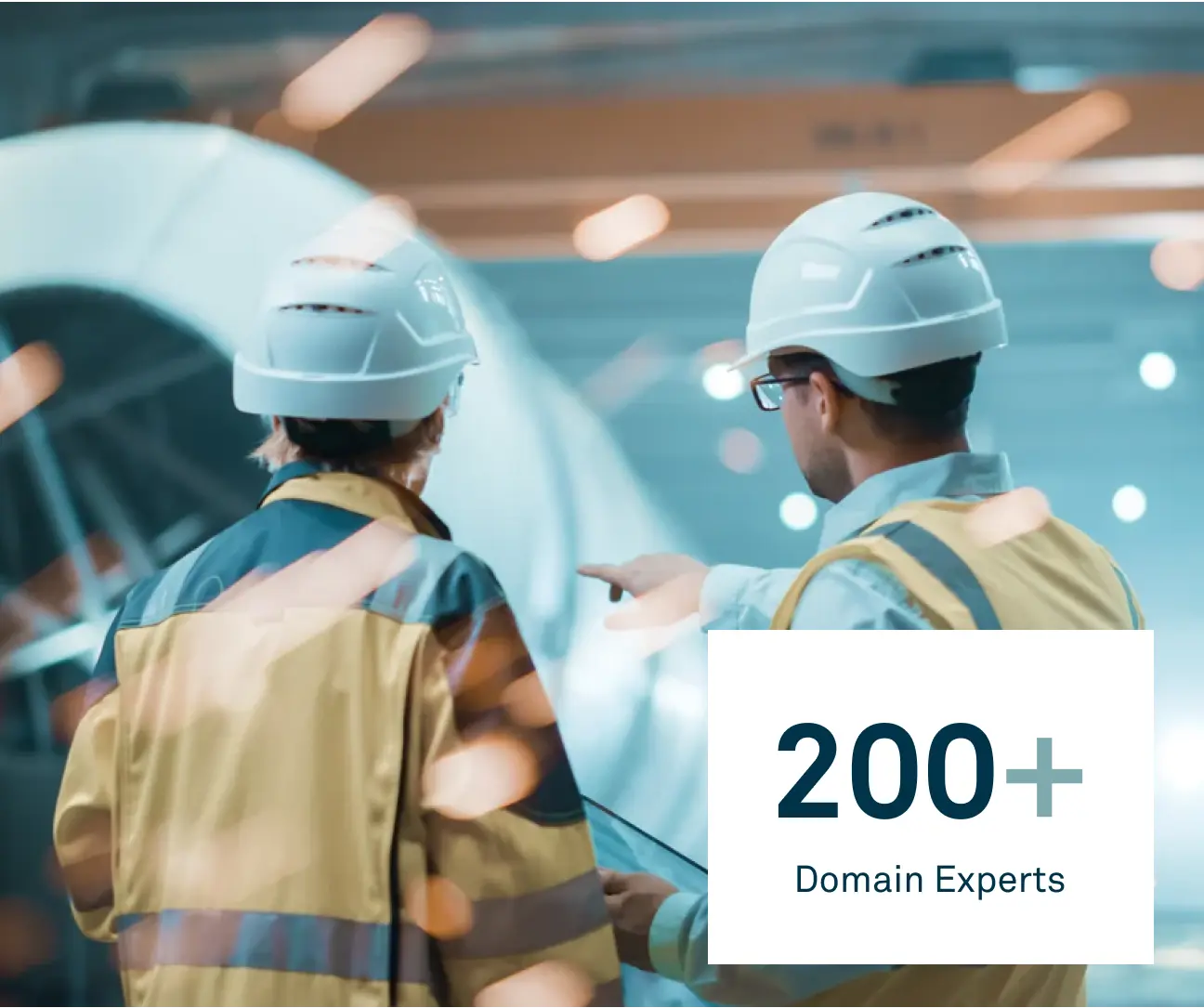
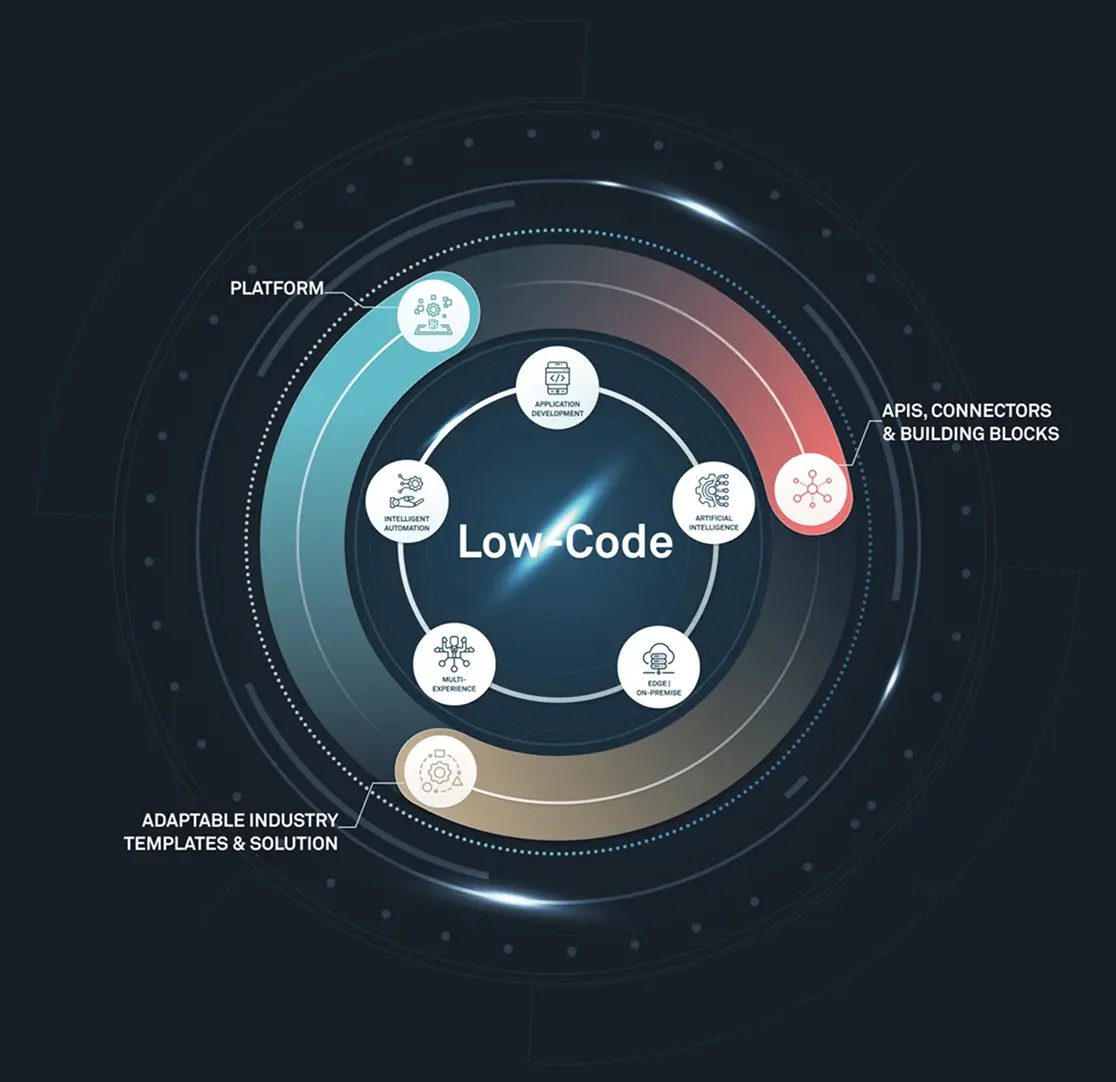
Maximizing PLM with Low Code and CLEVR's Expertise
Proper Product Lifecycle Management is what turns ideas into winning products (with the necessary support offerings and feedback loops). It's a systematic approach to managing a product’s entire lifecyle, from design and manufacturing to servicing and disposal. Importantly, it strengthens the collaboration between people, processes, and products, focusing on the big and small processes that make all the difference.
PLM stands at the forefront of Industry 4.0, integrating advanced technologies like AI, IoT, and MES. These integrations are paving the way for a smart manufacturing ecosystem.
CLEVR offers innovative solutions that enable manufacturers to effortlessly connect their digital processes with real-world operations.
Boosting the Manufacturing Ecosystem With AI and MES
Manufacturing Execution Systems
Manufacturing Execution Systems (MES) enhance Product Lifecycle Management by aligning shop floor execution with business strategy. They monitor real-time data on production orders, material consumption, quality metrics, and inventory levels, leading to improved efficiency and decision-making.
AI in Product Lifecycle Management
PLM uses machine learning for enhanced efficiency and streamlined processes, enriched by the strategic partnership between CLEVR and DFKI. Using data science, ML, and AI improves PLM so businesses can refine product development, reduce costs, and enhance overall efficiency.
Stories from our customers
See how businesses like yours are transforming with CLEVR.
Related Blog Articles
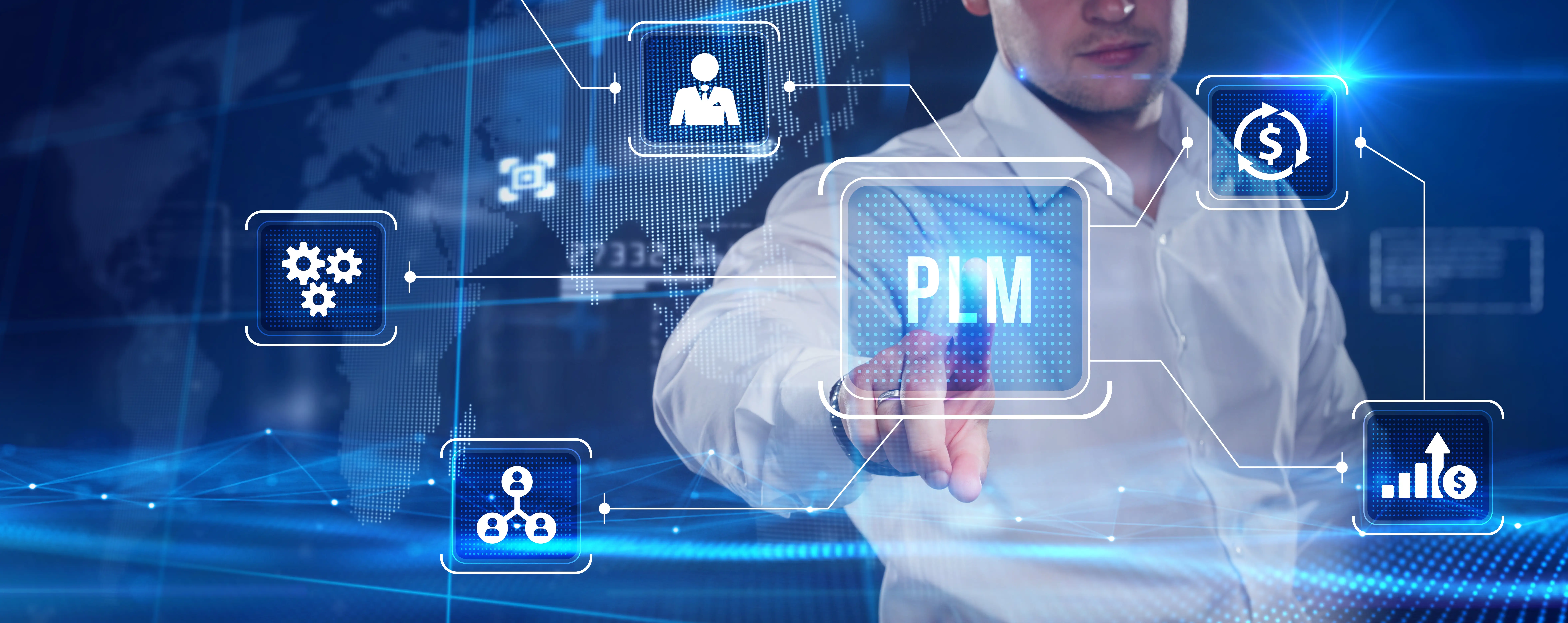
The right Product Lifecycle Management (PLM) platform can supercharge your company's engineering, manufacturing, collaboration, and time-to-market. Choosing the wrong one, on the other hand, can lead to costly integration challenges, poor user adoption, and a failure to realize the expected return on investment.
Among the leaders in the PLM space, Dassault Systèmes' ENOVIA and Siemens' Teamcenter are two of the most powerful and widely adopted solutions.
Each platform provides comprehensive features that serve customers by industry with specialized workflows. This guide provides a detailed comparison to help you make the best choice.
Short on Time? Here's a Brief Overview
- Teamcenter excels in complex manufacturing with best-in-class multi-CAD support and deep integration into production processes, making it ideal for large, diverse enterprises.
- ENOVIA's strength lies in its integration within the Dassault Systèmes 3DEXPERIENCE platform, making it a native fit for organizations using CATIA and other DS tools.
- The choice often depends on your existing technology ecosystem; aligning your PLM with your primary CAD and enterprise software vendor can prevent costly and complex integrations.
Side-by-Side Feature Comparison
A PLM system serves as the operational hub for all activities related to a product, from its initial concept to final retirement.
Teamcenter, from Siemens, is one of the most widely used PLM systems globally, recognized for its comprehensive capabilities and robust performance in managing complex manufacturing environments. Its architecture is designed for scalability and is well-regarded for its deep integration with manufacturing operations, as well as its exceptional support for a wide array of third-party design tools, making it a frequent choice for large, diverse enterprises.
Dassault Systèmes’ ENOVIA functions as the collaborative innovation engine of the broader 3DEXPERIENCE platform. Its primary strength is its native integration within this unified environment, creating a single source of truth that connects people, data, and processes. It’s often favored by design-centric organizations in industries such as aerospace and automotive, particularly those that utilize CATIA and other Dassault Systèmes applications.
To understand which platform might be right for your organization, it’s useful to compare how they approach important PLM functions.
Bill of Materials (BOM) management
A Bill of Materials is the complete list of all parts, components, and raw materials needed to build a product. Managing the BOM accurately is fundamental for coordinating purchasing, manufacturing, and assembly.
Teamcenter is built for deep manufacturing process integration, excelling at the complex task of reconciling engineering BOMs (eBOMs) with manufacturing BOMs (mBOMs). Its feature set is particularly advantageous for discrete manufacturers who need to manage make-versus-buy definitions and substitute parts in detail.
ENOVIA, by contrast, prioritizes a unified BOM within the 3DEXPERIENCE platform. Its strength is ensuring a single, consistent product definition is used across all Dassault Systèmes (DS) applications, from design to simulation. This is a considerable advantage for organizations heavily invested in the DS ecosystem that need absolute consistency, though it may require more configuration to achieve the same depth of manufacturing-specific BOM definition found out-of-the-box in Teamcenter.
Change management
Product designs are rarely static, and a formal process for tracking, approving, and implementing modifications is necessary to avoid errors and costly rework. Both platforms offer robust, industry-standard change management.
ENOVIA offers industry-standard Engineering Change Request (ECR) and Engineering Change Order (ECO) processes that often require minimal customization, making it a suitable choice for organizations seeking to adopt standard practices quickly.
Teamcenter provides highly configurable, guided workflow processes for managing changes, giving organizations greater flexibility to model the system precisely to their unique operational needs. Companies with established, non-standard change procedures will appreciate this versatility.
Document management
A product’s lifecycle generates countless documents—from technical specifications to compliance certificates. A robust PLM system must organize, secure, and control the version of every file. Here, the platforms offer different functional strengths.
ENOVIA has a deep, metadata-rich integration with the product structure. It supports documents with unique IDs, revisions, maturity states, and defined ownership, and it offers direct integration with CAD packages for version control of design files.
Teamcenter provides strong, core capabilities for document identification and version control, integrating with standard enterprise tools like Microsoft Office to manage related documentation. Its functionality is built to handle the essential tasks of securing, organizing, and tracking the progression of all files associated with the product lifecycle.
Quality & risk management
Ensuring product quality and complying with industry regulations are non-negotiable, and PLM systems are instrumental in embedding these processes into the workflow.
Teamcenter offers a dedicated, specialized "Teamcenter Quality" module, which functions as a comprehensive, standalone QMS with specific tools for Failure Mode and Effects Analysis (FMEA), audit management, and control planning. This modular design is a distinct advantage for organizations that require deep, pre-packaged quality management functionality.
ENOVIA integrates its quality and compliance tools across the entire 3DEXPERIENCE platform. This ensures quality metrics are visible and consistently applied across all disciplines, creating a more holistic view of compliance, though it may not have the same depth of specialized tools as Teamcenter's dedicated module.
Analytics & reporting
To improve processes, companies must be able to measure them. Analytics and reporting features within a PLM system collect data from across the product lifecycle to help identify bottlenecks and opportunities for improvement.
While both platforms provide analytics, Teamcenter offers an impressive ability to integrate data from diverse enterprise sources for comprehensive analysis. It's particularly powerful for organizations that need to consolidate reports spanning the PLM system, ERP, MES, and other business software.
ENOVIA's analytics are intrinsically tied to the 3DEXPERIENCE platform, providing detailed information from the data managed within that ecosystem. This is ideal for analysis focused on the product lifecycle within the DS environment, but may require more configuration for extensive external data integration compared to Teamcenter.
Collaboration & user experience
ENOVIA is designed to promote collaborative innovation through shared digital mockups and streamlined design reviews. Its web-based interface on the 3DEXPERIENCE platform is intended to be accessible from any device. User reviews for certain modules, like Engineering Central, have been positive regarding user-friendliness.
Teamcenter's user experience has been a topic of discussion. While the modern Active Workspace Client (AWC) offers an intuitive, role-based interface, some feedback on TrustRadius indicates the older Rich Client (RAC) is perceived as cluttered and outdated. The choice of client can significantly impact user adoption and customer service interactions.
Integration & Ecosystem Fit
Teamcenter is a central component of the Siemens Xcelerator portfolio, ensuring tight integration with Siemens tools like NX and Solid Edge for CAD, Simcenter for simulation, and Opcenter for manufacturing.
A key differentiator is its multi-CAD support, efficiently managing data from a wide array of systems, including CATIA V5, Creo, and SolidWorks. So, it's a strong choice for companies with a diverse design environment. Integration with ERP systems, such as SAP and Oracle, is well-supported through partner solutions.
ENOVIA's primary integration strength is its native connection to the Dassault Systèmes 3DEXPERIENCE platform. This creates a unified environment for companies using CATIA for design, SIMULIA for simulation, and DELMIA for manufacturing.
For organizations committed to the Dassault ecosystem, ENOVIA offers an integrated workflow and a single source of truth. Integration with third-party CAD and ERP systems often relies on solutions provided by partners.
Deployment, Scalability & Cost
Teamcenter offers exceptional deployment flexibility, including traditional on-premise, cloud-hosted (IaaS), and a full Software as a Service (SaaS) solution via Teamcenter X. This scalability makes it suitable for organizations from mid-sized businesses in the United States to the largest global enterprises.
While some user reviews mention high costs for certain licenses, a 2024 Total Economic Impact study by Forrester Consulting found that a composite organization using Teamcenter X could potentially achieve a 90% ROI over 3 years.
ENOVIA is primarily delivered through the cloud-native 3DEXPERIENCE platform, which offers SaaS, PaaS, and IaaS packages managed by Dassault Systèmes, simplifying deployment and maintenance. The licensing model is typically subscription-based per named user, with casual licenses available for part-time access. While pricing is customized, the cloud model is designed to lower the total cost of ownership by reducing internal IT overhead.
User Ratings & Satisfaction
On G2, Teamcenter holds a rating of 4.3 out of 5 stars from over 700 reviews, while ENOVIA has a 4.1-star rating from around 80 reviews. Teamcenter consistently scores higher in detailed feature comparisons for BOM management, document management, and data quality. On TrustRadius, Teamcenter has a score of 8.2 out of 10, where ENOVIA sits at 6.8 out of 10.
Common positive themes for Teamcenter include its robustness, stability, and strong integration capabilities. For ENOVIA, users praise its deep integration with CAD tools, such as SolidWorks, and its user-friendly interface for specific tasks. Both platforms have strong customer bases in the automotive and aerospace industries.
Choosing Based on Your Needs: Scenarios
The decision to switch platforms is significant, and your organization's specific profile and strategic priorities, as well as observations of recent customer movements, should guide your decision.
For large enterprises prioritizing deep manufacturing integration and robust multi-CAD support, Teamcenter is often the preferred choice. Its end-to-end lifecycle coverage and proven scalability are well-suited for complex, global operations. Current customers, such as Nel Hydrogen, have successfully implemented Teamcenter to automate and modernize their production processes.
For organizations deeply invested in the Dassault Systèmes ecosystem, particularly with CATIA, ENOVIA offers the most seamless and native PLM experience. The unified 3DEXPERIENCE platform eliminates many integration hurdles.
The CLEVR Support Framework
Selecting a PLM platform is only the first step. A successful implementation requires a partner with deep industry and technical expertise. CLEVR supports organizations through the entire process, from initial evaluation to long-term governance.
We provide platform-agnostic assessments to help you define your requirements and choose the solution that best fits your business goals. Our services include developing pilot projects, creating detailed cost models, and designing robust integration strategies. By focusing on adoption roadmaps and comprehensive training, we ensure your team can leverage the full power of your chosen PLM system.
Conclusion and Next Steps
Both ENOVIA and Teamcenter are formidable PLM platforms capable of managing the most complex product lifecycles. The best choice depends on your company’s strategic alignment, existing technology landscape, and core business priorities.
ENOVIA offers a deeply integrated, collaborative environment for those within the Dassault Systèmes ecosystem. Teamcenter provides a powerful, highly scalable, and manufacturing-focused solution with exceptional openness to a multi-CAD world.
Your next step should be to conduct a thorough internal assessment of your functional requirements, integration needs, and long-term vision. Engage with implementation partners who can provide expert guidance and help you navigate the complexities of a PLM transformation.
If you lean towards Teamcenter, CLEVR is ready to help you make it work from day one. Get in touch with CLEVR’s experts to help define your PLM strategy and ensure the platform you have selected works with your needs in mind to drive your business forward.
Research Methodology
This comparison is built on extensive analysis of official vendor documentation, independent industry reports, and aggregated user feedback from trusted software review platforms like G2 and TrustRadius. We prioritize recent information and user reviews to provide a current and accurate perspective on both PLM software platforms.
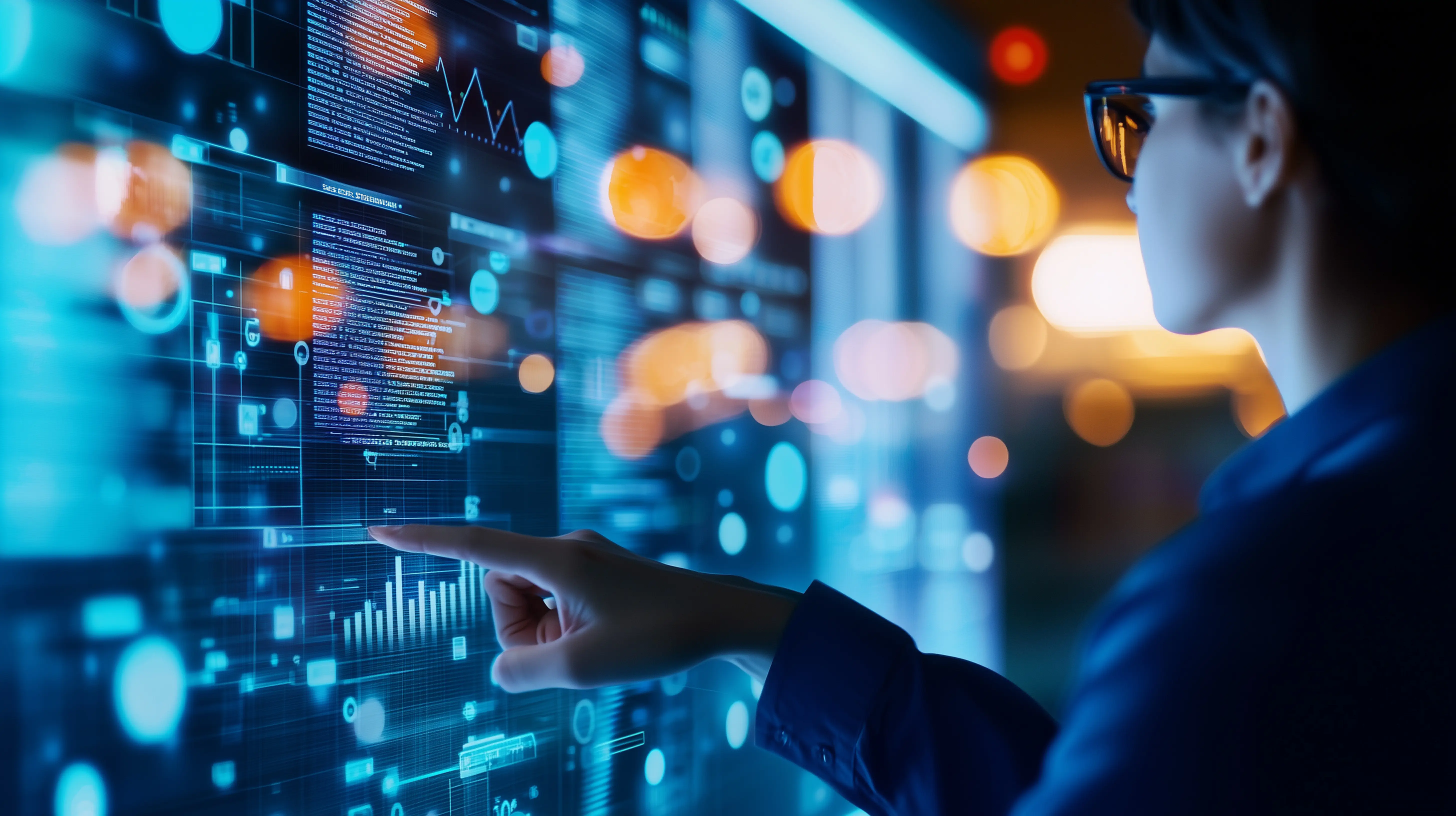
From Fragmented Systems to Future-Ready: CLEVR’s Step-by-Step PLM Integration Guide
Product lifecycle management (PLM) software plays a key role in managing every aspect of your manufacturing process—from design to delivery. However, a PLM can only do its job properly if it serves as a single source of truth for your organization.
If your company’s manufacturing process is fragmented across multiple PLM platforms and other systems, you’re not alone. Many organizations begin with a streamlined PLM but lose their digital cohesion over time due to mergers, growth, and internal process changes.
The good news is that you can re-establish your PLM as a unified, organization-wide platform through integration—and CLEVR PLM engineers Joana Nunes Silva and Lars Erik Haajhem have deep experience helping companies achieve just that. We gathered their insights to help you transition from fragmented systems to a future-ready state, step by step.
Why Is PLM Integration Necessary?
Before we dive into the steps to integrate your PLM system, it’s important to understand how a fragmented environment can arise, why it’s a problem, and how a PLM solution can help.
How fragmented systems develop
According to Joana and Lars Erik, one of the most common reasons organizations end up with multiple PLM systems is the acquisition of smaller companies, each with its own pre-existing PLM systems and ways of working. The goal in these cases, as they put it, is “to go from two companies using two systems to one company using a single platform for production.”
They also see many situations where companies begin taking on more customers without having a PLM system in place. These businesses often resort to ad hoc methods to manage a growing volume of data, resulting in disconnected systems and disorganized digital files. In such cases, it becomes necessary to have a PLM system that can seamlessly integrate existing data.
Whether through acquisition or accelerated growth, both scenarios are ultimately unsustainable. They require a PLM system to serve as a unified platform, one that enables clear communication of product designs, easy information sharing with suppliers, and accurate specifications for manufacturing processes. Relying on disconnected systems can lead to poor collaboration during design, manufacturing delays, and quality control issues.
Fragmentation also poses a barrier to keeping systems up to date. As Lars Erik and Joana point out, this is a major challenge because “these applications are evolving really, really fast.” Organizations without unified, standardized systems miss out on the latest upgrades, and implementing advanced features in the future becomes more costly due to the need for custom development.
Why your business needs an integrated PLM system
An integrated PLM system dramatically improves the entire manufacturing process, from collaborating on designs to managing supply chains to creating and delivering finished products. It reduces costs, speeds up time to market, and improves product quality.
Joana and Lars Erik emphasize these benefits of PLM: “With a PLM, you have much more traceability of your products and your assets. You start to really see your product and your full data, and a PLM can solve all the duplicates and issues and inconsistencies that your company had before. You can see the full history of your product, which [you] might not have had knowledge about before doing this integration.”
They also point out that having this structured data has a real impact on your business’s bottom line and ability to innovate. “You can see how your product has gone from an idea many years ago to how it's living right now. It gives you an overview of what your business is actually selling and what you can make more money on. The rewards from having a streamlined PLM system come very fast.”
Integrating Your PLM System: Step-by-Step Guide
Based on their experience helping companies deploy, integrate, and customize PLM systems, Joana and Lars Erik offer a four-step guide to PLM integration:
Step 1: Assess the current PLM environment
The first thing companies need to do to achieve a streamlined PLM is to understand their current situation and how a PLM can help. The integration process can vary significantly depending on a company's current stage in its digital journey.
For example, if your organization aims to unify several PLMs that are already in use, “you have to make some decisions,” Lars Erik and Joana continue. “Do you move all the data to one of your already existing applications? Or do you create a new application and migrate your data there?” Which approach is better for your business will depend on whether one of your PLM platforms fully meets your business’s needs and whether it is easily upgradeable as new features become available.
If your company doesn’t have a PLM at all, you’ll need to select a software vendor and identify what data needs to be migrated to the new system. Joana and Lars Erik recommend Siemens Teamcenter because of its advanced collaboration tools and customizability for a wide range of industries. They also praise its steady stream of updates, which help ensure businesses future-readiness.
Here partnering with PLM experts can be incredibly beneficial. “We have experience working with a lot of different customers across different industries,” say Lars Erik and Joana. “That knowledge helps us advise businesses on how to align the way they work with how their PLM software can best be used.”
Step 2: Develop new PLM systems in parallel
Instead of rolling out a new PLM all at once, Joana and Lars Erik recommend that companies should develop their integrated system in the background. “By not touching the legacy system and instead setting up a completely new PLM, we can work in parallel. Users can still use the existing applications while we develop a new system based on a new way of working. In time, we can migrate different products into the new system and train employees how to use it.”
This approach has a number of benefits. It minimizes disruption to your company’s operations while the integrated PLM system is being developed. The new system can also be thoroughly tested and fully functional before it’s rolled out across your organization, and individual products or teams can be migrated to the unified PLM one at a time, making the change management process much simpler.
There are several ways to manage this parallel development. One example Joana and Lars Erik provide is creating an integration layer—a database that receives information from multiple existing PLM and other applications—using low code. “You can then integrate or migrate data from your legacy environments to the new environment.”
Using a low code platform such as Mendix can simplify integration work, especially when dealing with multiple legacy systems, and can provide added flexibility, making PLM systems even more powerful.
Step 3: Train employees on your new PLM
Before new PLM systems can be rolled out, team members need to be trained on how to use them. This is crucial for ensuring employees can hit the ground running with your integrated PLM and earn buy-in, ensuring engineers, product designers, and manufacturing leads actually use the system. Without this buy-in, employees could end up using workarounds that result in more fragmentation.
“We do a lot of training,” Joana and Lars Erik add. “Usually, before we even have projects starting, we show how Teamcenter works out of the box, the different modules in Teamcenter, and what capabilities the different modules offer. This gives them a touch and feel for the system before they start using it.”
Training offers an opportunity to identify needs that can be incorporated into the development and software configuration process. “We go into this discovery period where we sit together and we discuss the behavior of the system to understand how it fits with their way of working. We also ask about the requirements that different teams have so that we can configure the system to work as best as possible to meet them.”
Step 4: Deploy and scale
Once your integrated PLM system is ready and employees are prepared for the switchover, you can deploy the new software. However, instead of rolling out the new PLM across your entire organization all at once, it’s a good idea to introduce it to individual teams first or implement it for specific projects. That way, you have an opportunity to identify any speed bumps or bugs before they cause significant issues.
Once you’re confident in the system, it can then be deployed more widely and scaled across all your business’s projects. At this point, you can back up data from legacy PLM systems that will no longer be used and decommission them.
Lars Erik and Joana emphasize the importance of listening to feedback from employees once the new PLM is implemented. “We get quite a lot of good feedback,” they say, which can help identify opportunities for new features or additional integrations.
Tips for a Smooth PLM Integration
In addition to sharing details about the approach they use for PLM integration, Joana and Lars Erik offer several tips to ensure your integration process is as smooth as possible:
Get your team on board by letting them know how their collaboration impacts the rest of the business.
Changing PLM systems often requires employees to adapt to new ways of working, which can be difficult, especially if they’re coming from an acquired company with a completely different software approach. Invest time in explaining the broader value of the change, and involve teams early to increase engagement and reduce resistance.
PLM is changing incredibly fast. So make sure that the platforms you build are ready to be upgraded with new features and integrated with additional systems in the future.
Choose a PLM solution that can grow with your business. Your system should be capable of integrating with future PLM tools, third-party platforms, or compliance software—especially in cases of future mergers or supply chain expansion.
Configure your systems to fit in your framework so that you always have that possibility of upgradeability.
One of the key benefits of integrating fragmented PLM systems is that it enables the use of standardized software platforms with regular software updates. So, while adapting your PLM to your business’s specific needs is important, it’s equally important to remain within the bounds of your software.
Be patient and go step by step to achieve a good end result.
Moving from multiple applications to one common system is not an overnight process. Take a phased approach, set realistic expectations, and focus on long-term results rather than quick wins.
Integrating Your PLM System: Step-by-Step, Side-by-Side With CLEVR
For organizations looking to go from fragmented systems to a single, unified PLM system, CLEVR serves as your expert partner. We offer a step-by-step approach guided by experts like Joana and Lars Erik, and we work by your side throughout the entire integration process.
Ready to streamline your PLM and ensure your business is future-ready? Check out our PLM solutions and customer success stories to learn more.

Product Lifecycle Management (PLM) is essential for success in the consumer products and retail industry, offering remarkable benefits for retailers. As Product Lifecycle Management (PLM) tailored specifically for retail, it efficiently manages retail products throughout their lifecycle, from concept-to-commerce. Studies have shown that by implementing DLM solutions, retailers can reduce physical sampling by up to 70%.
With the rise of unified retail commerce, omnichannel strategies, and increasing volumes of digital data, implementing robust PLM practices becomes crucial to enhance data organization, accessibility, and security, leading to improved operational efficiency and enriched customer experiences.
Throughout this article, we will discover the key components of PLM implementation in Consumer Products and Retail and explore how CLEVR empowers retailers to manage their processes efficiently and thrive in this dynamic industry.
CLEVR: Revolutionizing CP&R with Limitless Fashion Innovation
CLEVR offers a specialized SaaS solution known as PLM for Consumer Products and Retail, designed specifically for retail, apparel, footwear, and accessories brands. The platform boasts innovation by establishing an end-to-end digital value chain, completely automating the design-to-sales process for its users.
Tailored to meet the unique requirements of each brand, CLEVR's highly configurable solution breaks away from the limitations of traditional fashion seasons. It streamlines the entire production workflow, encompassing ideation, planning, design, merchandising, development, sourcing, sampling, and manufacturing.
By serving as a powerful partner, the platform empowers brands to stay ahead in the fast-paced fashion landscape. Brands can expect to experience a radical reduction in time-to-market, up to 80%, and get significant cost savings in production, driving them towards sustainable success.
Key Benefits of CLEVR’s PLM solutions for Retailers
Traditionally, Fashion brands have typically been limited by fixed seasonal cycles, restricting their creative exploration. However, with CLEVR's PLM solutions, these limitations reduce, and a new era of unrestricted innovation begins.
- Workflow Efficiency
CLEVR's PLM serves as an effective platform in streamlining the entire production workflow. From the initial spark of an idea to its grand manifestation on the runway, every step is optimized for maximum productivity. Automation and seamless collaboration enable fashion brands to quickly meet demand and bring their creations to life, giving them a competitive edge in the market.

- Effective Communication:
Recognizing that teamwork is the key to success, this digital solution encourages effective communication and cooperation among designers, merchandisers, developers, and other essential stakeholders. By aligning their visions, they ensure that the final product embodies the essence of the brand and creates a lasting impact on the fashion world.
- Digital Collaboration and Style Specification:
CLEVR's PLM offers Digital Collaboration Solutions that boost ideation with dynamic digital mood boards for instant inspiration sharing. Advanced Color Management ensures color consistency, expediting product development and the centralized platform effortlessly handles all aspects of products such as colourways, grading, design intent, measurements, and SKUs, ensuring maximum efficiency.

- Sourcing Process Optimization
Optimized sourcing workflows are enabled through automated tech packs and global vendor collaboration, resulting in quicker time-to-market, reasonable pricing, and improved product quality. CLEVR's PLM also offers Smart Collaboration Solutions with Mendix's low-code multi-experience capabilities, activating processes seamlessly on any device and fostering collaboration among teams.
The true power of CLEVR's PLM lies in empowering brands to embrace the future of CP&R and Fashion fearlessly. As the industry continues to evolve rapidly, this innovative solution opens doors to limitless possibilities for fashion brands seeking to make a lasting impact. By automating processes and nurturing creativity through collaboration, CLEVR's PLM paves the way for an exciting era of fashion innovation.
So, fashion-forward brands, are you ready to break free from tradition, streamline your creative process, and thrive in the dynamic fashion landscape? The runway is yours, and the possibilities are infinite. Contact Us today, and step into the world of limitless fashion with CLEVR's PLM solution.